E-motor efficiency optimisation, according to ZF
Ahead of the 11th Advanced E-Motor Technologies 2024 conference (Munich, 5-8 March 2024) Automotive IQ interviewed Fabio Dohr, Head of Platform Portfolio Electric Vehicle Drives at ZF Group to understand how the complete powertrain system can be optimised from a system-level approach.
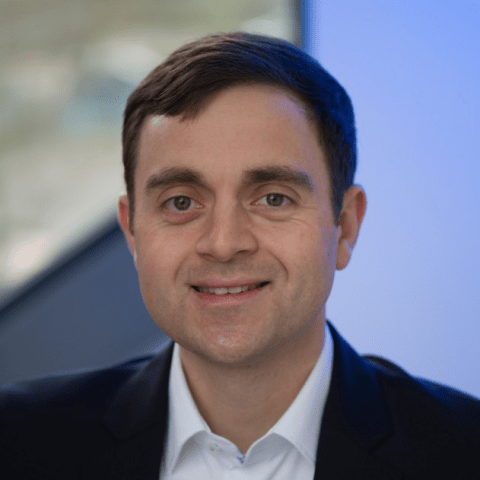
The industry has moved from designing the e-motor as an individual component in the system, to adopting a system’s approach and designing the e-motor to fit into the wider system. Though beneficial in many ways, system integration can present some challenges to the motor producer, so it’s important for companies to know the most effective ways to design the e-motor in relation to the entire system.
Designing the e-motor for system efficiency
What are the key considerations when designing the combined unit of the motor, power electronics, and the inverter to ensure optimal performance?
“Designing a system is always a trade-off to fit customer requirements in the best way. All components interact with and influence each other. So, it’s not as easy as ‘taking the best motor, inverter etc.’ to get the best system in the end. First, it is important to translate customer requirements into system requirements and to check if they fit into our modular kit. Performance, efficiency, packaging, weight, and of course, cost are key categories in this instance. With these, engineers can start defining the system architecture and to design the individual components.”
How can a system’s approach benefit the overall efficiency of the powertrain, and what role does the design of the e-motor play in this?
“As mentioned, all components interact with each other. And if you understand the system and the parameters you have, you can use these interactions for optimisation, but what does that mean? By changing parameters in the inverter, like the maximum current or switching frequency, you directly influence the e-machine and possibly its design. Take the e-machine: by changing speed and torque, you directly influence the reducer and its differential, which are required to transfer the mechanical energy to the wheel. So, changing one parameter will affect many other components of the system. In the end, it is an optimisation task with countless parameters. Something which can’t be done with a pencil and a calculator. That’s why we use system simulation tools to find the optimum out of several thousands of possible variants.
When looking at the e-machine, it’s the central element in the powertrain, which converts electrical energy into mechanical energy. And it’s the major step towards influencing efficiency. Hence, the design of the e-machine itself has a huge effect on the overall powertrain efficiency. But it is not only about efficiency. There are many other requirements to be considered, which make the design of an e-machine such a complex task.”
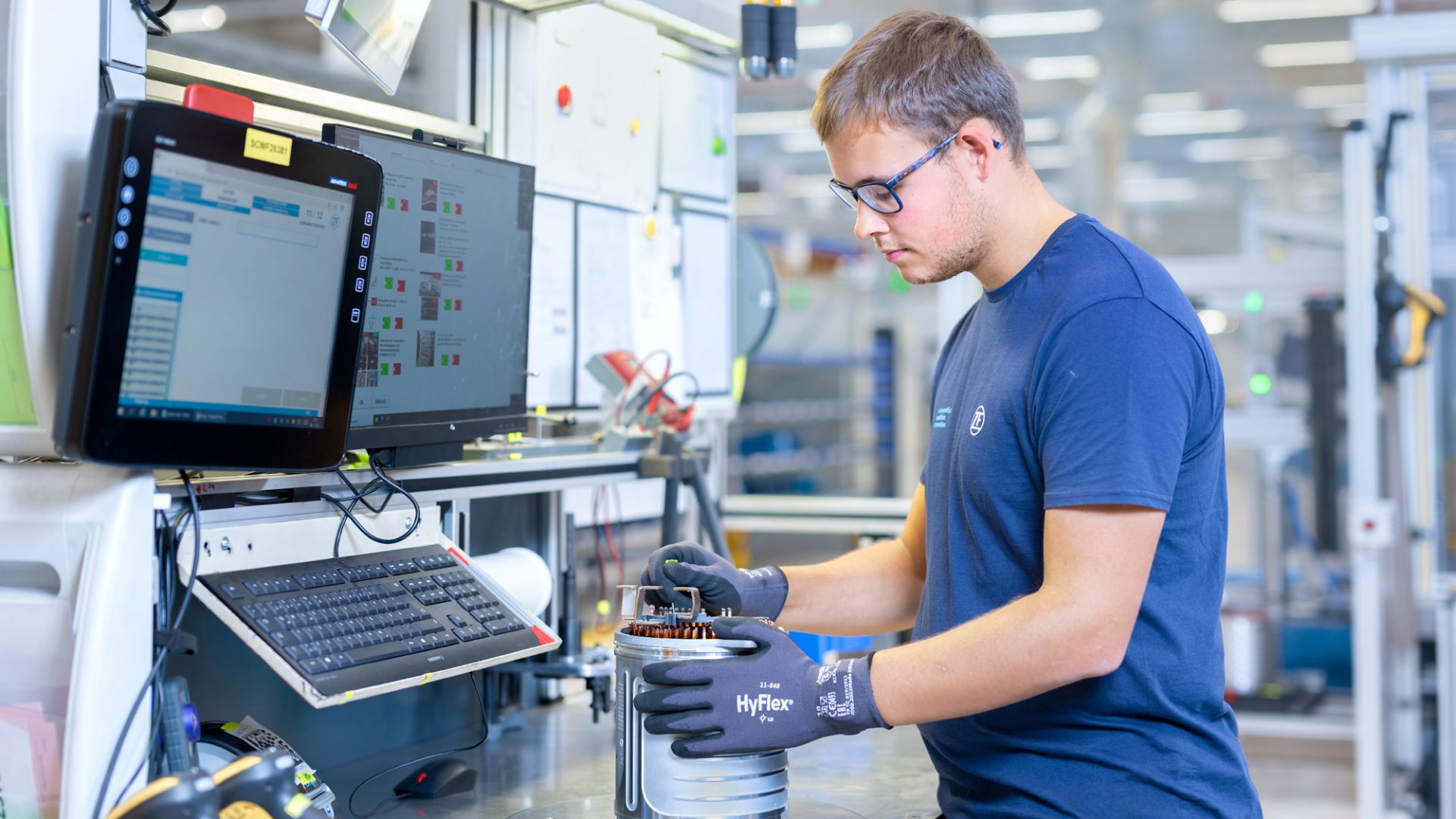
As the industry shifts towards a system’s approach, what challenges do OEMs and Tier-1s commonly face in integrating the e-motor into the wider system?
“Let’s start with a non-technical challenge, and that is cost. Electric vehicles are still a relatively new technology which means that cost optimisation is still on a different level than in the established ICE world. In addition, the high impact of the battery on total vehicle cost also has an effect on the powertrain, as all components in the vehicle have to somehow contribute to a cost compensation.
Apart from that, there are several e-motor technologies available at the moment. The question is, will there be a consolidation and if so, in favour of which technologies? Furthermore, there is not much standardisation yet. As a result of that, there is still a broad variety of requirements, like when it comes to packaging. This can be challenging, especially for a Tier-1, as reuse across customers is crucial to be successful, but on the other hand, this is a great chance to create scale effects. Typically, something an OEM has much more limit in. We at ZF tackle this challenge with a modular kit approach which is the basis for all our customer projects.”
Could you share some practical solutions or strategies to overcome challenges related to system integration and ensure seamless collaboration between different components?
“I can only speak from a ZF-perspective, and I think that we have a great advantage. We are capable of developing and producing everything inhouse: reducer, electronics, e-machine, and with that, of course, also the complete system. Our teams work together cross-functionally from the very beginning and onwards, not only within R&D, also within production. This reduces interfaces and enables us to make changes very quickly by finding the best solution across all components. That’s enabling coherent systems instead of what I tend to call ‘Lego-systems’.”
In your experience, how does designing the e-motor in relation to the wider system contribute to increasing overall system efficiency?
“To make it short, massively. As it is converting electrical energy into mechanical energy, it is the heart of the powertrain. And it is the component where you can lose most of your efficiency, if you’re not doing it right.”
Are there specific design principles or techniques that can be employed to maximise the efficiency of the e-motor within the broader context of the powertrain system?
“Of course, we have specific design principles within ZF. But that’s exactly the point, where we think our knowledge comes into play and what differentiates us from others. So, I don’t want to disclose too many details on that. But what I can say is that we are intensively using simulation technologies to optimise the e-motor design. Not only as singular component, but also within the entire system scope.”
Can you elaborate on the role of inverters and motor controllers within the e-motor technology ecosystem?
“If we referred to the e-machine as the heart of the powertrain system, the inverter is its brain. And considering that the inverter consists not only of electronics, but also of software, this becomes obvious. With all the functions which are implemented today – and there are much more innovations to come in future – electronics and software contribute massively to the overall system functionality. And it is not only the basic controlling functions for the e-machine, it is about safety, security, comfort, efficiency and more. For example, we have software functions which optimise the NVH behaviour of the entire system. That enables us to reduce hardware requirements for other components, which is great.”
How do these components fit into the overall design strategy, and what considerations should be considered to optimise their performance in conjunction with the e-motor?
“As I mentioned before, we strive to optimise the system generally, not only on component level. The paradigm of systems engineering, ‘the whole is greater than the sum of its parts’, is really essential in this case. In the end, it is all about the right trade-off. Not only technically, also from a cost-, production- and security of supply-perspective. Last year, marked ten years since the E-Motor Technologies conference first took place in Germany. Not only was it a milestone year, but it was also our biggest, most value-led event to-date with attendance numbers surpassing all expectations.”