PetrolValves and Bosch Rexroth join forces for the safe transport of hydrogen
Bosch Rexroth and PetrolValves have signed a Memorandum of Understanding to collaborate on the electrification of subsea systems for the storage of captured carbon and for the safe transport of green hydrogen produced offshore using renewable energy.
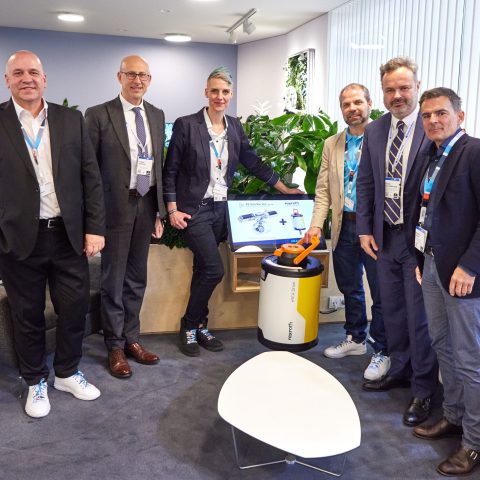
Bosch Rexroth and PetrolValves have signed a Memorandum of Understanding to collaborate on the electrification of subsea process valves with high Safety Integrity Level requirements, such as Subsea Safety Isolation Valves (SSIV). Both companies are already working on a solution that connects PetrolValves subsea valves with the Rexroth actuator eSEA Drive. Operation and control are carried out via simple 24 V DC electric power supply. The new development will reduce the investment and operating costs of subsea systems for the storage of captured carbon (CCS/CCUS) and for the safe transport of green hydrogen (H2) produced offshore using renewable energy.
The biggest challenge in the use of offshore systems for the capture and storage of CO2 and the use of green hydrogen (H2) is to reduce the total cost of ownership. A significant lever for cost reduction is electrification, for example through the eSEA actuators developed by Bosch Rexroth, which cover all safety-relevant movements at water depths of up to 4,000 meters. They are a particularly economical alternative to the hydraulically driven actuators that have been normally used. Until now, especially, large subsea process valves with high Safety Integrity Level (SIL) requirements could not benefit from electrification due to the lack of a suitable and affordable drive solution.
The agreement between Bosch Rexroth and PetrolValves covers the development and qualification of new valve variants, such as a 10- or 12-inch ball valves, as well as the promotion of these solutions to the market. “Together, we will offer to the operators the opportunity to introduce innovative all-electric technologies that will reduce the acquisition and operating costs of their plants, minimizing the energy consumption and protecting the environment,” said Miguel Vallcorba Piera, Chief Commercial Officer of PetrolValves.
Both companies have already implemented this solution using an eSEA Drive from Bosch Rexroth to electrify a subsea 5’’ gate valve, and a full-scale prototype is currently in the final phase of qualification tests to reach Technology Readiness Level (TRL) 4 by mid-2024.
“Our solution eliminates the entire hydraulic system for valve actuation: central hydraulic power units above water and kilometers of hydraulic pipes. This simplifies the design and speeds up the engineering and commissioning of offshore systems, thus improving the overall response time from the control system and the safety level,” says Alexandre Orth, Head of Subsea Automation Systems, Bosch Rexroth. In addition, machine-learning based condition monitoring adds further operational and safety benefits.