Poppe + Potthoff: a material specially developed for use in hydrogen applications
Poppe + Potthoff has designed an alternative specifically for pipes and rails in hydrogen applications
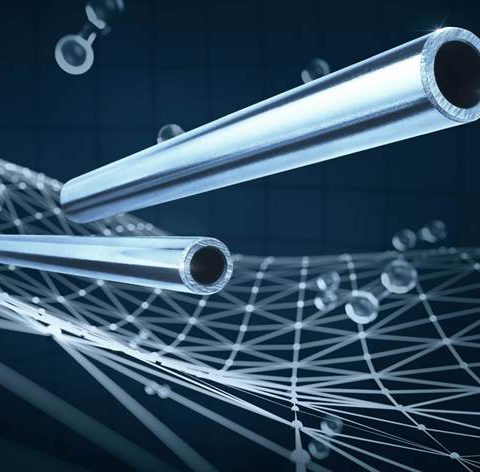
Poppe + Potthoff has designed an alternative specifically for pipes and rails in hydrogen applications. Hydrogen systems for mobile or industrial applications are made up of multiple, interacting components. To ensure reliable storage and transport of the gas within the systems, these components, such as pipes, valves, or rails, must be extra robust and resistant. The components used in hydrogen applications are often manufactured from austenitic stainless steel to fulfil these demanding requirements.
This solution, however, has some disadvantages. For example, stainless steel has relatively low strengths, so the components must be designed with greater wall thicknesses for higher pressure resistance. This increases their weight, while the higher material input leads to higher component costs.
One way to counter these disadvantages is to use carbon steel for hydrogen applications. As a global operator the Poppe + Potthoff Group has many years of experience in the manufacturing of components made of carbon steels from the field of diesel applications. Poppe + Potthoff has designed an alternative specifically for pipes and rails in hydrogen applications: PPH2.
PPH2 is an alloyed carbon steel with high mechanical properties, which are further enhanced by the innovative PPSH annealing treatment. These special properties allow the production of thinner-walled components (compared to stainless steel) and thus a reduction in weight while increasing the availability of hydrogen pipes and rails. The composition of PPH2 meets the requirements of the EIGA (European Industrial Gases Association) for pipes and containers for the transport of hydrogen. External corrosion protection is provided by a zinc-nickel coating.
PPH2 was already tested by TÜV Saarland/TÜV Rheinland in accordance with DIN EN ISO 11114 in 2021 and approved for use in hydrogen applications under EU Regulation (EC) No. 79/2009. With the successful testing according to ANSI/CSA CHMC 1-2014, a material compatibility test according to another set of regulations has now been added. In a cooperation with the testing institute TÜV SÜD Chemie Service GmbH, Poppe + Potthoff was also able to have the material tested according to a newly developed testing methodology. The results of this test also confirm the successful outcome of the CHMC1 test.
As a development partner for its customers, Poppe + Potthoff independently develops and produces components such as pipes or rails made of PPH2 for up to 700bar nominal pressure. Pipes, H2 rails (manifolds) and interfaces have been successfully certified in PPH2 by an independent testing institute according to EC79 and successfully tested according to the maximum requirements of HGV3.16.