«We see room for modern diesel engines». Our interview with AGCO Power CEO Juha Tervala
«We know that in high power heavy-duty applications, diesel engine will be the main power source in a long time and therefore we see still room for modern diesel engines. The family will include 4- and 6-cylinder versions and, since the beginning of the project, alternative fuels have been considered», said CEO Juha Tervala.
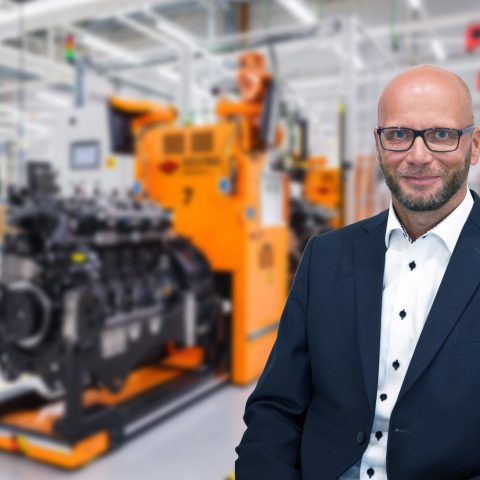
For the last ten years at least, AGCO Power has been the power source of Agco Group’s tractors. CEO Juha Tervala gave us several interesting hints, talking about the recent investments made at Finland’s Linnavuori production plant as well as bout the company’s strategy following the Covid outbreak. Something really interesting came up, indeed.
How has AGCO Power faced the pandemic outbreak? How has all this affected the company’s results in 2020?
Spring 2020 was naturally challenging. Many key component suppliers, especially in Europe, were closing manufacturing due to Covid-19. Our purchasing team did great work and we didn’t have to stop the production due to component shortages. On the other hand, our customers suffered a lot and couldn’t continue production and our engines were not needed and therefore we had no production for couple of weeks
The recovery was very fast especially in AG and our engine production ended up to the budget level. Other industries suffered longer time and those customers were typically 20 percent below budget 2020.
How AGCO Power CEO Juha Tervala sees 2021, and beyond
What’s AGCO Power’s view for the current year?
We know already that 2021 is not only recovery year, but a boosting one! We have adjusted our forecast higher and higher month by month. The second half of the year will be very busy and again also very challenging not least due to component situation in the market. We, like many others, face problems to get components including semiconductors.
AGCO Power is strongly committed to the captive market, then supplying the machines belonging to the brands of the AGCO Group. Do you foresee a stronger commitment to the free market in the future?
Yes, indeed. During AGCO ownership, we have been growing mainly together with AGCO by replacing external engine brands by captive engine and we have still some room to grow further. We have though quite fresh strategy to grow also with new third-party customers and we believe to be successful with that.
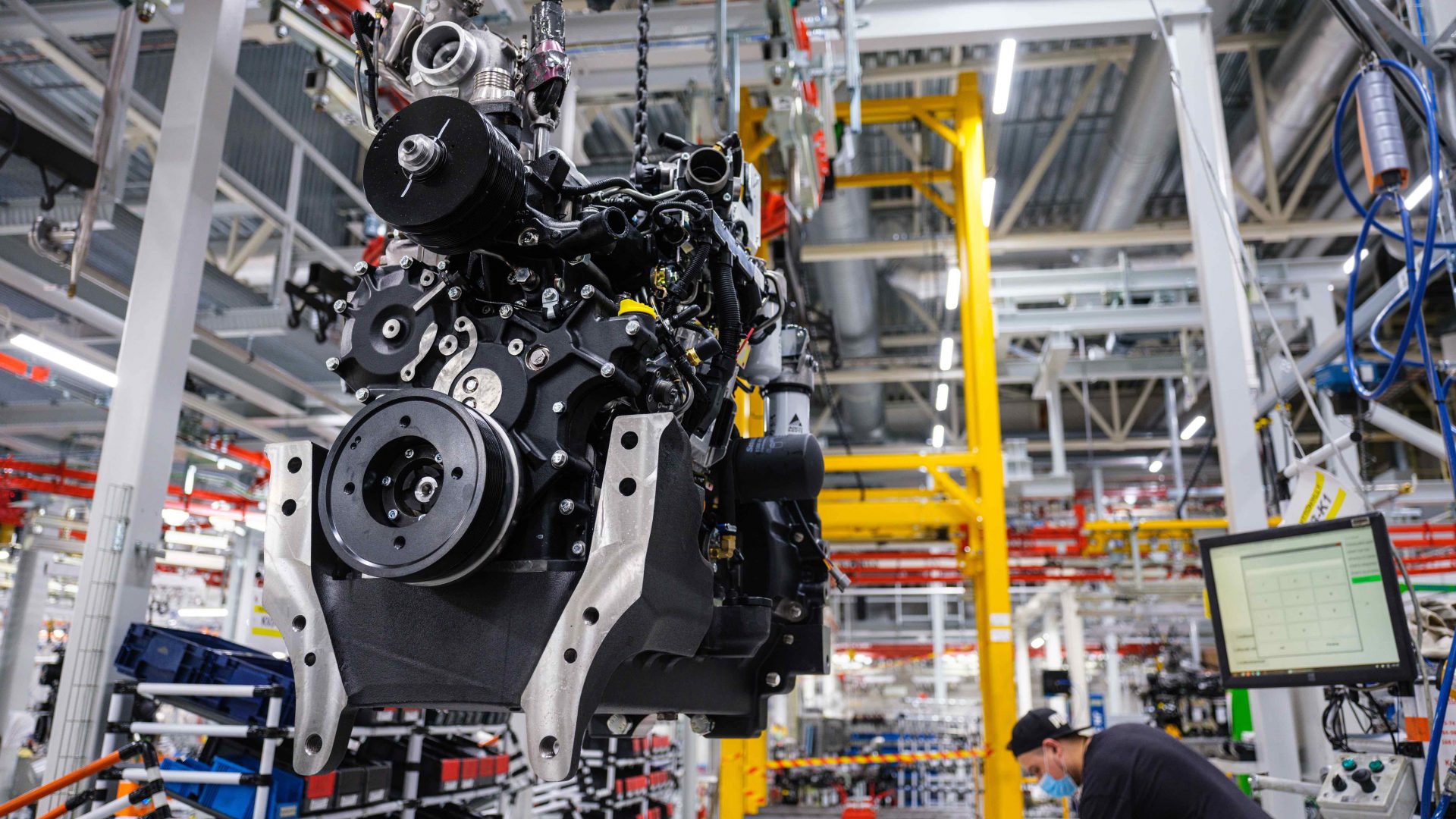
You’ve been talking about a new engine family to be released by the end of 2022. Could you share some information about it?
We know that in high power heavy-duty applications, diesel engine will be the main power source in a long time and therefore we see still room for modern diesel engines. The family will include 4- and 6-cylinder versions and, since the beginning of the project, alternative fuels have been considered. We have many branches of research related to alternative fuels. Full electric is not for us, but we are already testing gas and hydrogen.
The challenges of digitalization
The world of agricultural machines is facing a strong evolution based on connectivity, data and smarter machines. In such a scenario, which are the main challenges for engine manufacturers?
We have super good and most modern solutions for connectivity, telemetry and remote control, but at the moment we use them only in testing purpose. The cost is still too high for serial vehicles. It will go down in the future, for sure.
In January 2007, we paid a visit to the plant. The Sisu imprint was still visible at the time. What traces of the imprinting and the Finnish identity have remained?
We have not given up any Finnish identity, even though we are part of a large American group. We no longer use the brand Sisu, but all the qualities contained in this very Finnish word are still a part of us all: perseverance, honesty, openness, hard work, diligence. The best way to prove it, is to spend the evening in our company’s traditional sauna…
What habits of the parent company’s usually American approach have you transferred at Linnavuori?
AGCO is the best possible family for us. AGCO relies on our expertise and has invested significant sums in our factory and products. We have adapted our operations in line with AGCO’s strategy.

We’ve just talked about a very relevant investment made by AGCO in engine manufacturing in Linnavuori. Could you please give us some more details about the improvements expected in the manufacturing processes?
We’ve already Implemented a new logistic center for incoming goods, a new storage area with narrow aisle forklifts as well as a new fully automatic storage system delivered by KNAPP. Our internal logistics has been enhanced with Mobile industrial robots (MiR), we have a new flexible assembly line with hybrid cells and AGVs, new electric hot test cells, new painting line and shipping area.
The next steps will see a new machining line for key components as well as a renowned training center.
Automation in Linnavuori
How would you define the degree of process automation within AGCO Power’s Finnish factory?
The automation level is very high, I would say highest in our kind of industry as for production volume. The benefits go from productivity improvement to labor cost savings, up to more stable quality and good work environment, mainly in terms of ergonomics for employees.
Which robots are currently employed in the assembly area?
The robots we use are made by ABB. We have though our own very capable team that takes care of design of fixtures, programming, installation and so on.
What about AGVs in intralogistics?
We have already several mobile industrial robots (MiR) transporting goods from logistic center to the assembly line. We have two different models carrying 1000 kg or 200 kg. They are ‘more clever’ than traditional AGVs, which are travelling along define routes. Our mobile robots scan continuously the area around them and select best possible routes.
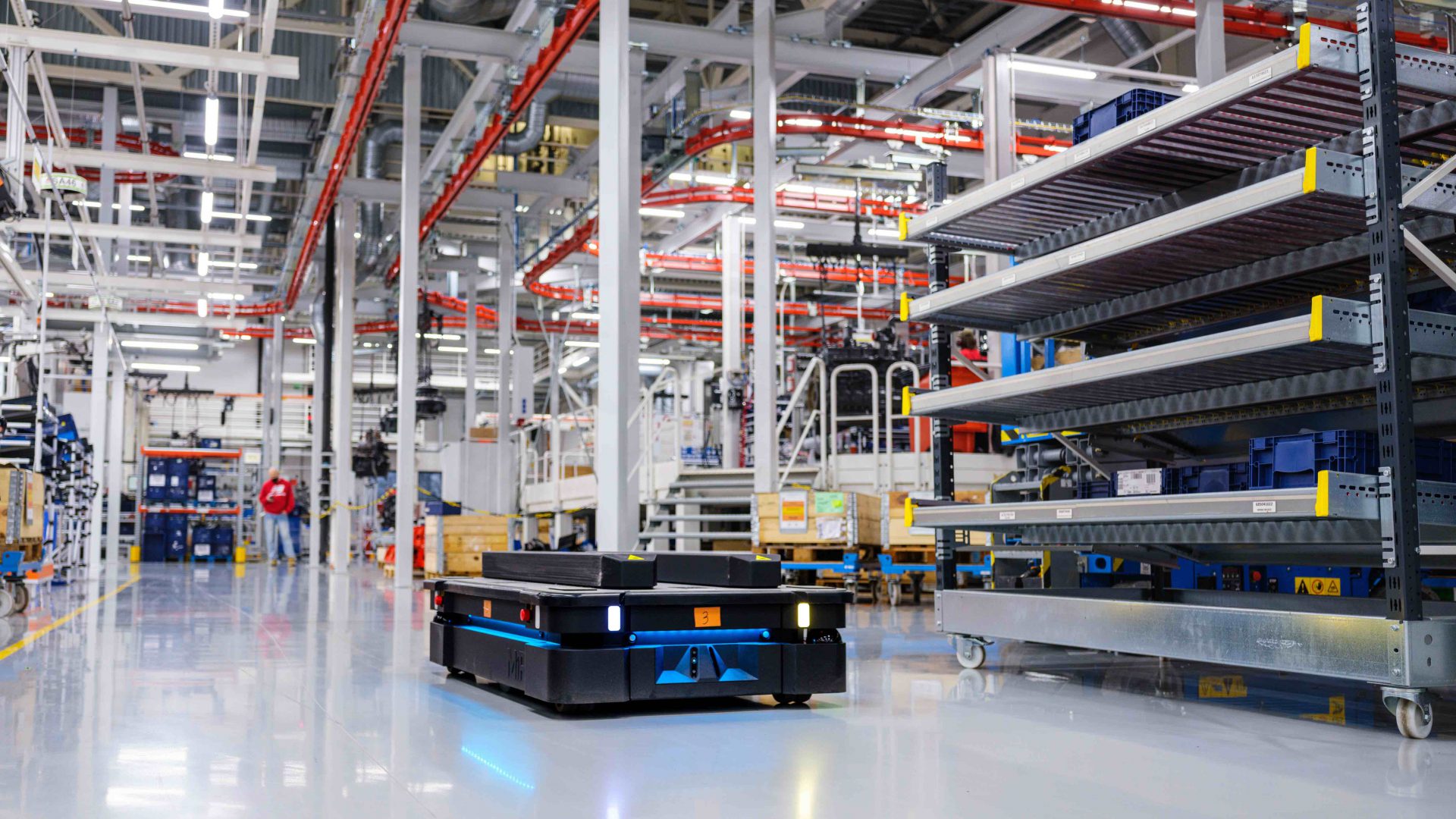
Are you planning to employ collaborative robots? Do you believe they might fit in your manufacturing process?
In our new assembly line employees and robots are working in the same stations in seamless collaboration. The concept is similar as with cobots, but due to heavy components the safety measures must be different. We have laser safety nets around the engine, making sure that in no conditions accidents can happen. In our system, which we call ‘hybrid cells’, human beings and robots work together.
Talking about engine production, how do you think it might change in the near future? Is advanced automation a good option to make the processes smoother and ensure a highest repeatability?
We have been ‘automation believers’ for several decades. Robots were used in machining as early as the 80s, and even in assembly, robots have been working for 20 years.
Today’s themes are flexibility, consistent quality and employee well-being. Automation is an excellent tool for continuous productivity development. On the other hand, we want to take advantage of people’s superior qualities and have them in this kind of assembly tasks. Heavy and monotonous work steps should be automated in first place. In addition to machining and assembly, a good example is painting, which we have automated a long time ago. Our new painting line has two robot lines and their programming is handled flexibly using virtual reality technology.