Kohler KSD: genesis and opportunities
The KSD series (aka Kohler small displacement) raises Kohler’s quotation below 19 kilowatts. Guido Franchi, Product manager of Kohler Engines, told us about this project
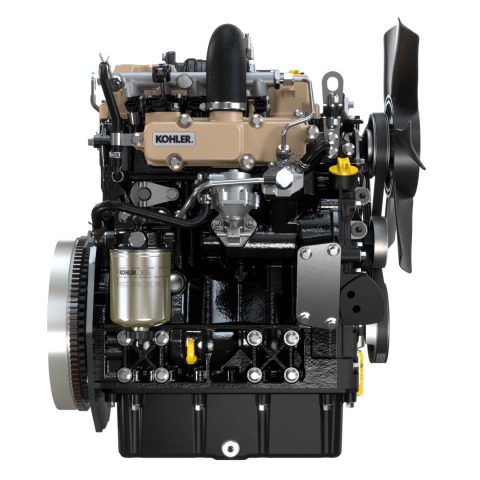
We asked Guido Franchi, Product Manager of Kohler Engines, to investigate the reasons for this compact Kohler KSD 1.4-liter series, which completes the metamorphosis of Kohler’s proposal, after the successful addition of the KDI series. You will find the complete interview in the January-February issue of DIESEL.
What are the market demands for units like KSD?
After the KDI, this engine certainly represents one of the most ambitious projects of Kohler Engines: it is in fact a completely new engine, therefore it is in no way derived from the existing series, the FOCS and the CHD. With the experience of the KDI and FOCS on our shoulders, we have tried to create an absolutely innovative engine, which meets the Stage V and Epa Tier 4 Final regulations and those that are coming into force in several other countries. The “node” of 19 kilowatts constitutes a limit for which choices must be made: above this power range, thus providing superior performance, after-treatment is mandatory. We decided to design a diesel engine that would deliver less than 19 kW of power. The strategic choice that some of our competitors have made is to de-calibrate the existing engines, paying a pledge to the inevitable loss of performance, especially in terms of torque. Starting from the real needs of the market, we have instead developed an innovative technology (the reference is primarily to the injection system, editor’s note) that has allowed us to set up an extremely compact platform, one of the vectors of attractiveness required by installers. Although the displacement is 1.4 liters, the overall dimensions are smaller than those of competitors.
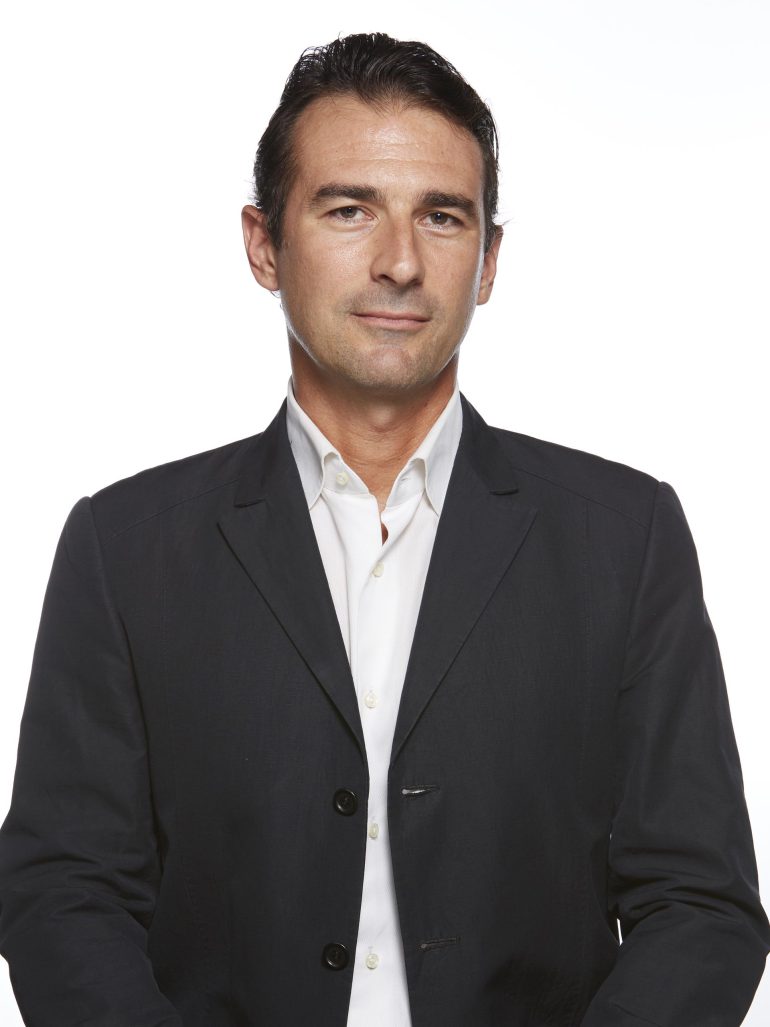
What elements of rupture and competitiveness with respect to engines which are widely tested in this range?
With the dimensions of an engine of 1.1 liters of displacement, we were able to package a 1.4-liter unit, with extremely high torque: 90 Nm at 1,800 rpm in the aspirated version, which rises to 105 Nm in the turbocharged version and 120 Nm in the one with aftercooler. In this way we were able to combine compactness and performance, especially in terms of torque at low revs, and power at low revs, which is usually achieved with much larger engines, typically 1.5 or 1.7 liters. By designing a unit from scratch, we wanted to create an engine that was best in class thanks to a very technological approach, as demonstrated by the fully electronic injection. There are not many electronic motors of this size. The electronics must represent an advantage for the customer, therefore it must not lead to an increase in costs or complications in terms of installation, so we have focused a lot on flexibility: we are able to offer all the advantages of the electronic motor without impacting, from the point of view of customer, on the ease of installation. In a certain sense, we offer a “drop-in”solution, in which a mechanical engine already present on the machine can be easily replaced. This means that the same engine is offered, for example, with two wiring interfaces: with the standard one the customer can continue to use his own analog dashboard, or his own mechanical lever (we offer a potentiometer on the engine).