ZF TempAI cares the temperature of the e-motors
ZF TempAI delivers temperature data from the heart of the e-motor
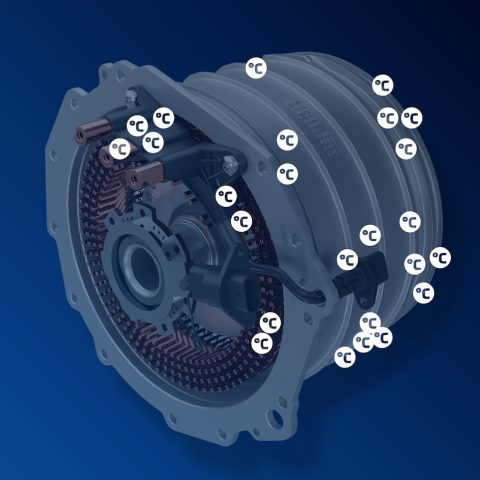
TempAI was conceived by ZF to mitigate one of the worst drawbacks of electric motors: the temperature inside the electric motors. We’re talking about a 15% more accurate temperature control. An improvement driven by artificial intelligence.
Too much heat fot the e-motors? ZF provides TempAI
With its AI-based TempAI solution, ZF is integrating a new method that takes temperature management in electric drives to a new level. TempAI is based on a platform that automatically generates physically based models from measurement data and makes them operational in a very short time. Existing control units are sufficient, as the AI models used require low computing resources. This leads to very cost-efficient implementation in series production. “This technology enables us to further increase the efficiency and reliability of our drives. At the same time, TempAI demonstrates how data-driven development can be not only faster, but also more sustainable and more powerful,” said Stefan Sicklinger, Head of AI, Digital Engineering, and Validation in R&D, ZF. The AI-based technology is ready for series production and available for the new generation of ZF electric motors. “We are proud to bring this innovation into series production and thus making a significant contribution to more efficient e-mobility,” said Otmar Scharrer, Head of Development for Electrified Powertrain Technology. ”TempAI is a real technological breakthrough for the temperature management of electric drives.”
About the WLTP cycle and rare earths
More precise temperature prediction enables more targeted control right up to the thermal operating limit. The result: up to six percent more peak power and a verifiable increase in efficiency in the WLTP cycle, the global standard for realistic driving emissions. During dynamic driving – as for example, on the Nürburgring Nordschleife – energy consumption is reduced by 6 to 18%, depending on the load point. The optimized thermal design allows significant quantities of heavy rare earths to be saved. At the same time, the development time per project is significantly reduced: from several months to just a few days. During the development of electric drives, AI helps to understand and record processes inside the electric motor for which there is no physically reliable model for cost or time reasons.
Pros and Cons
ZF is not afraid of the challenges. According to the official, the temperature inside a rotor can only be measured directly during operation at high cost. However, there is a wealth of measurement data that is systematically recorded during extensive functional tests on the test bench and later in the test vehicles. This includes temperature values from the environment, such as from the oil pan, and the rotor speeds. The various possible operating points and their temporal progression result in millions of data points. These depend on whether and when drivers call up full power or coast along at walking pace. AI algorithms are “trained” to filter out precisely those dependencies that are particularly significant for temperature changes in the rotor and stator.