Volvo in the quarry is more sober than ever!
Volvo in the quarry doesn’t mean just Volvo Trucks. Volvo Penta is on the move to the fuel saving also powering a crusher. The stage is in Sweden, both the characters speak the same language, which helps to find mutually beneficial solutions. Volvo in the quarry, under the Swedish flag The second player is quarry […]
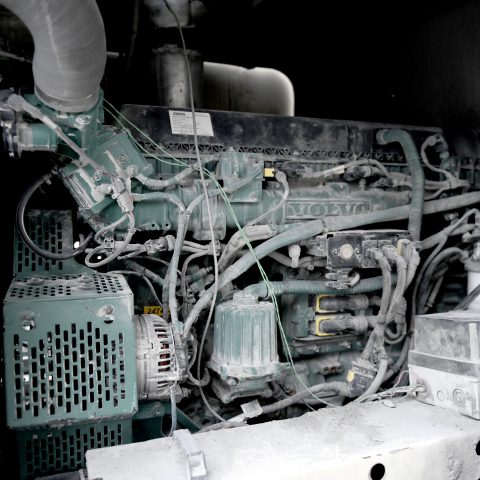
Volvo in the quarry doesn’t mean just Volvo Trucks. Volvo Penta is on the move to the fuel saving also powering a crusher. The stage is in Sweden, both the characters speak the same language, which helps to find mutually beneficial solutions.
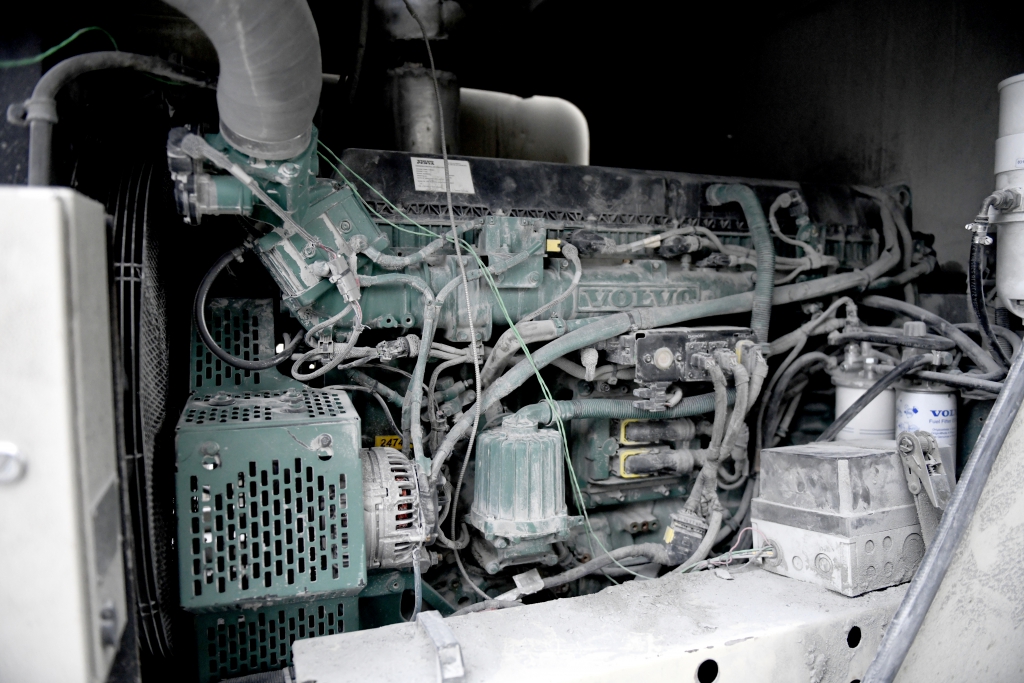
Volvo in the quarry, under the Swedish flag
The second player is quarry and recycling company Dalby Maskin, at their site in Uppsala, where is based the Scandinavia’s oldest university. Since 2010 Volvo Penta has been field-testing engines there, starting with a Stage 3B engine, moving to Stage IV and Stage V. According to Dalby Maskin statements, by switching its four crushers and a screener to Volvo Penta engines, it’s saving over €100,000 a year in fuel costs.
«After seeing how reliable and fuel-efficient the engine was during the field test, we knew it made financial sense to repower our other crushers and make the switch from a Volvo Penta competitor’s engine to a Volvo Penta model,» explains Jesper Sundström, Quarry Operations Manager at his family’s business, Dalby Maskin. «Volvo Penta had some great ideas about how to reduce fuel consumption, noise, and rpm (revolutions per minute) with a smaller engine while still getting the performance we needed – and they were right. We went from this competitor’s 15-liter engine to a Volvo Penta 13-liter engine. Since making the change, we’ve cut fuel consumption by up to 20 liters per hour (l/h). Previously, the service interval was 250 hours but now we have a 1000-hour interval between oil changes. And thanks to lower engine revs and smaller engine displacement, we don’t have to change the air filter that often. Within a couple of years, the engines pay for themselves – so there is a good business case.»
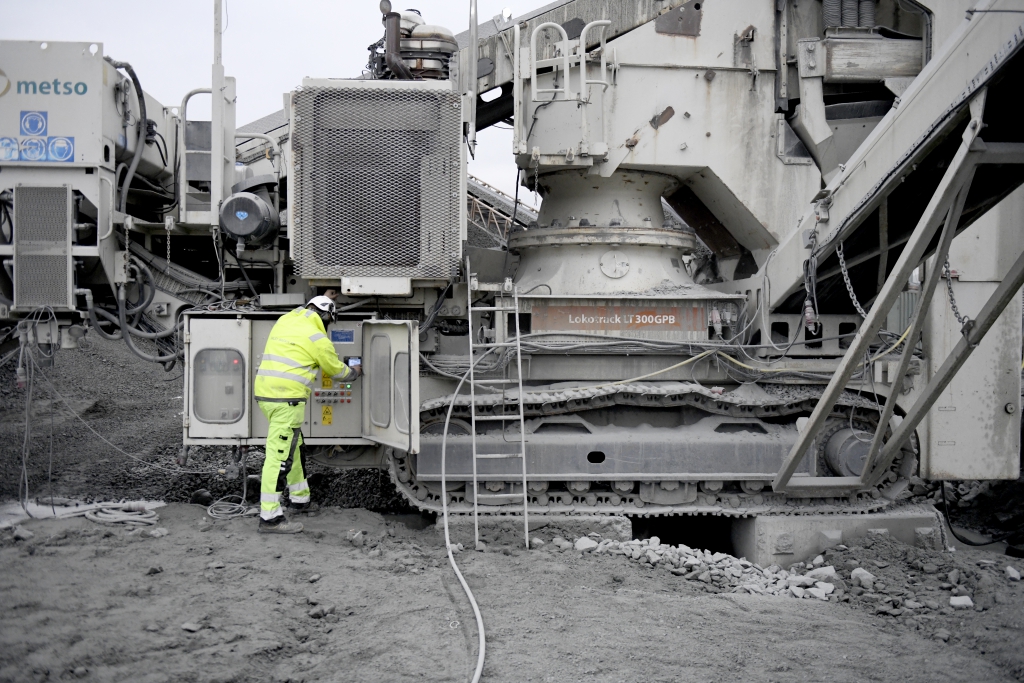
«We changed the size of the engine to see the difference between the D5 versus D8, as we thought the machine was over-powered for its application and workload,» explains Andreas Nyman, Manager Field Test, and Data Management at Volvo Penta. “«We also changed the hydraulic pumps so we could reduce the rpm from 1900 to 990. With these changes, we managed to decrease the fuel consumption from 11.6 l/h to 7.5 l/h. This is a significant reduction which saves the customer a lot of money, is better for the environment and doesn’t compromise performance. This is why we work with customers to find the right size engine for their application and usage, to maximize fuel efficiency and uptime.»
The Penta point of view
As they say from Guthemburg, “Volvo Penta has tested seven engines with Dalby Maskin over the last ten years. During this time, the company has also bought Volvo Penta engines to repower other equipment at the site. Currently, Volvo Penta is field-testing two engines at the quarry: a D13 Stage V, which is powering a Metso crusher, and a D5 Stage V, which is powering a screener. Testing started on the D13 in 2017 and so far, it has clocked up around 7,000 hours. The screener was originally repowered in 2015, switching from a competitor’s engine to a Volvo Penta D8 Stage III. In 2017, this was changed to a D8 Stage V, and last year it was replaced with a D5 Stage V – which has already clocked up around 2,000 hours.”