Steven Bell and BorgWarner turbochargers
Together with Steven Bell, Director of Sales for Commercial Vehicles at BorgWarner, to better understand the world of turbochargers
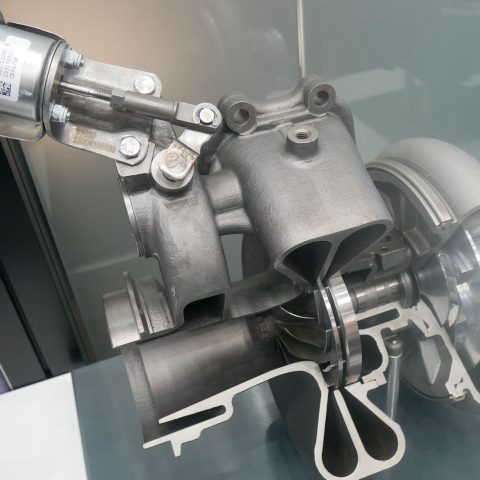
To cap off our quartet of in-depth features on BorgWarner at bauma, we’re welcoming Steven Bell, Director of Sales for Commercial Vehicles. He’s here to discuss turbocharging, joining us after Alessandro Benedetti‘s earlier references to BorgWarner’s turbocharging products.
The latest development in turbochargers, as explained by Steven Bell
“The latest unit incorporates several high-efficiency features aimed at pushing overall turbo efficiency toward 70%, a target the company refers to as HET70. A key enabler is a ball bearing system that reduces friction and improves responsiveness. The compressor side includes a newly developed vane diffuser that increases air handling efficiency, while the turbine side features a fixed nozzle ring with integrated vanes to optimize flow and energy recovery. A special coating at the compressor inlet reduces the clearance between the compressor wheel and the housing, further contributing to efficiency gains and fuel economy. Both the turbine and compressor wheel geometries have been refined extensively to extract as much performance as possible from each component.”
What about materials?
“Material choices remain largely conventional for diesel applications. The turbine wheel is made from Inconel, a nickel-based alloy capable of withstanding high temperatures, while the housing is cast iron with molybdenum and silicon for added strength. Since combustion temperatures in diesel engines are not expected to rise significantly, there has been little need for new material developments in this area.”
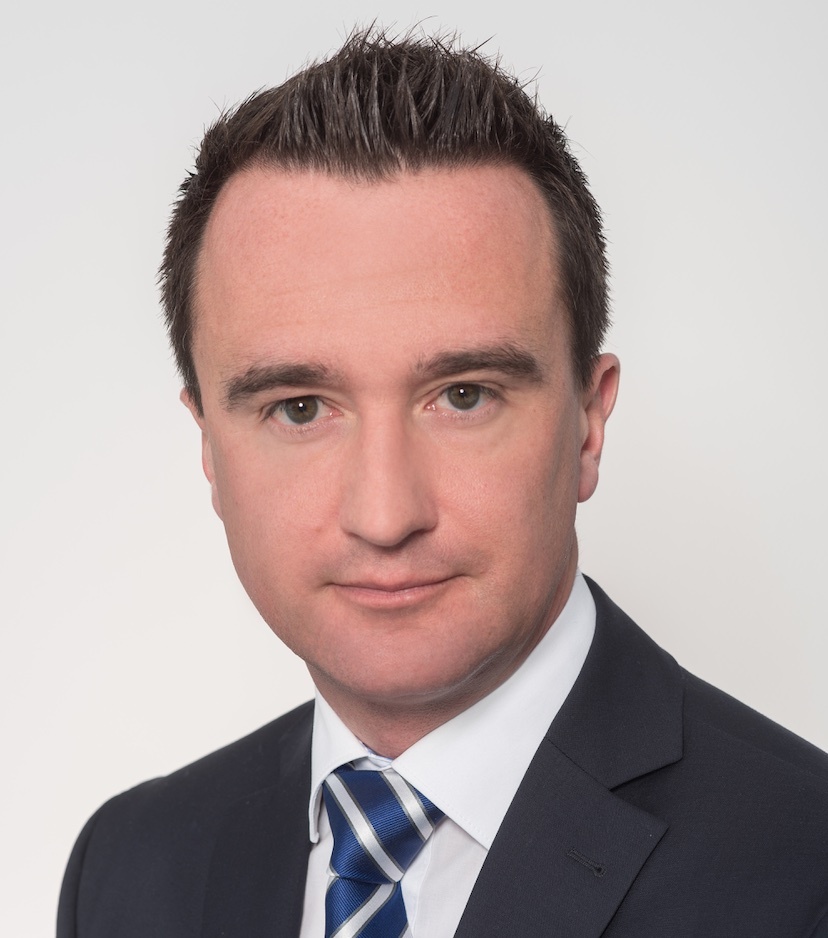
What changes does hydrogen bring?
“Hydrogen combustion introduces new variables. The stoichiometric air-fuel ratio changes dramatically, requiring substantially more air to enter the engine, which in turn affects the sizing of both turbine and compressor wheels. In addition, hydrogen combustion produces lower exhaust temperatures, reducing the energy available to drive the turbine and likely necessitating smaller turbine dimensions. There have also been concerns about hydrogen’s potential corrosiveness and its effect on lubricants or interaction with turbine housing materials. However, multiple tests with customers have shown no adverse effects so far, and BorgWarner considers its turbochargers ready for hydrogen combustion engines. That said, the market is not yet prepared for large-scale hydrogen adoption, primarily due to challenges related to on-board storage. In extended-range trucks, for example, replacing a conventional 1,100–1,200-liter diesel tank with compressed hydrogen would require space equivalent to 13.5 cubic meters of gas—nearly 10% of the payload. Discussions with OEMs in both on- and off-highway segments have confirmed these limitations.”
Finally, a window on the near future
“Looking ahead, BorgWarner expects diesel to remain dominant for the near term, with alternative fuels gaining traction as a viable alternative. The company believes the pace of innovation will make small but meaningful applications possible within the next five to seven years, and their new turbocharger platform is already proving itself ready for that transition. Tests with synthetic fuels also have been successfully completed, further confirming the unit’s versatility.”