Lhyfe: green hydrogen today, not tomorrow
Lhyfe has an ambitious goal to achieve: to make offshore renewable hydrogen a reality, by demonstrating the reliability of an offshore electrolyser
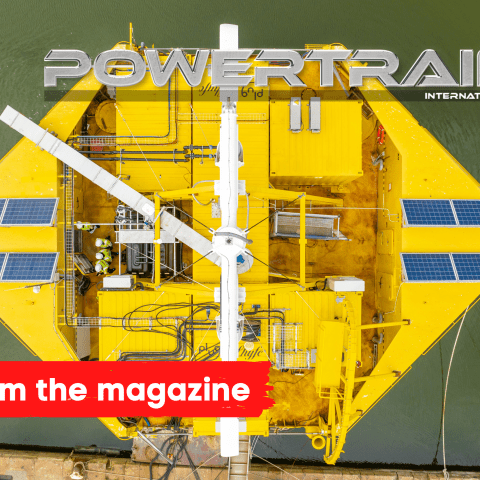
Lhyfe and its partners share an ambitious goal: to make offshore renewable hydrogen a reality, by demonstrating the reliability of an offshore electrolyser. This represents a world first at a time when initiatives for offshore hydrogen production are emerging across Europe. The world’s first offshore hydrogen production site, set up by Lhyfe in collaboration with Plug Power, Chantiers de l’Atlantique, Geps Techno, Centrale Nantes, Eiffage Energie Systèmes, Le Port de Saint-Nazaire and Kraken Subsea Solutions, is operational on the SEM-REV site from September 2022. The offshore test site meets all the criteria (MRE presence, harsh environmental conditions) to validate offshore hydrogen production technology before moving towards large-scale industrial deployment in order to have an additional installed capacity of around 3 GW by 2030-2035, offshore.
We talked about this project and much more with Thomas Créach, Lhyfe’s technical director. First of all, let’s retrace the way that led Lhyfe to the idea behind this project. “Everybody understands now that we have an issue on our planet which is called global warming,” states Créach. “If we want to have a future for our children, we need to stop this situation. Hydrogen is not the only solutions but is one of the solutions we have to decarbonize mobility and industry usage. Lhyfe was born to prove that this solution is feasible today, not tomorrow: we can produce green hydrogen now with renewable sources. That’s why in 2017 we launched this company in Nantes and we first deployed a site in the west coast of France, which is already in operation now.”
In September 2021, in fact, Lhyfe opened the world’s first industrial site with a direct link to a wind farm and seawater supplies for electrolysis. Located in Bouin in the Vendée, the site can already produce 750 kW or around 300 kg of green hydrogen a day (1 MW). This is set to rise to 1 tonne per day to meet growing demand.
Bouin’s green hydrogen is supplied to public and private clients in the mobility sector, including a hydrogen station owned by SYDEV (Syndicat départemental d’énergie et d’équipement de la Vendée) at La Roche-sur-Yon to fuel heavy vehicles (buses, household waste trucks, service trucks) and the hydrogen distribution stations on one of the Lidl distribution group’s logistics platforms to fuel its maintenance trucks.
“With our first onshore project, we have already proved that renewable green hydrogen is feasible today. Now we are developing the same kind of production site in other areas, so by 2024 we will have 55 MW deployed everywhere in Europe, and 200 MW by 2026. In 2019, at Lhyfe we were only eight, now we are around 130-140 people. Lhyfe shares are listed on Euronext Paris regulated market since 23 May 2022 and this gives us the financial capability to deploy faster and faster all these potential sites.”
What are the main applications to which Lhyfe supplies hydrogen, manufacturing plants or e-mobility?
“We deliver hydrogen for both uses. For example, in France we deliver each day to a logistic manufacturing (for hydrogen forklifts), to steel and glass industry, and to mobility (mainly truck and bus). Our main goal is to deliver renewable green hydrogen. So we have a pipeline of projects of around 9,8 GW in Europe onshore. We are investing in offshore because, as I said, if we want to massively produce renewable green hydrogen, then we need massive renewable sources. In offshore we have wind farms which are between 20 and 50 times bigger than the onshore windfarms, the availability of electricity is between two and three times more available than onshore and the price of electricity is quite interesting to produce hydrogen. More than that, offshore you have a potential production capacity which is more than 18 times the energy demand today onshore. The first production site, in operation since 2021, represented the first step of our strategy, while the second was inaugurated in September 2022.”
After the pilot site, where Lhyfe already produced the first kilograms of renewable green hydrogen at quay and then at sea, operating automatically, in the most extreme conditions, the company has voluntarily set the bar high by installing its production unit on a floating platform, connected to a floating wind turbine. The Sealhyfe platform must therefore meet several major and unprecedented challenges, including performing all stages of hydrogen production at sea, i.e. converting the electrical voltage from the floating wind turbine, pumping, desalinating and purifying seawater, and breaking the water molecules via electrolysis to obtain renewable green hydrogen; managing the effects on the system of the platform’s motion; enduring environmental stress because Sealhyfe will have to survive the premature ageing of its parts (corrosion, impacts, temperature variations); and, last but not least, operating in an isolated environment. The platform, in fact, must operate fully automatically, without the physical intervention of an operator, except for scheduled maintenance periods which have been optimally integrated from the design phase.
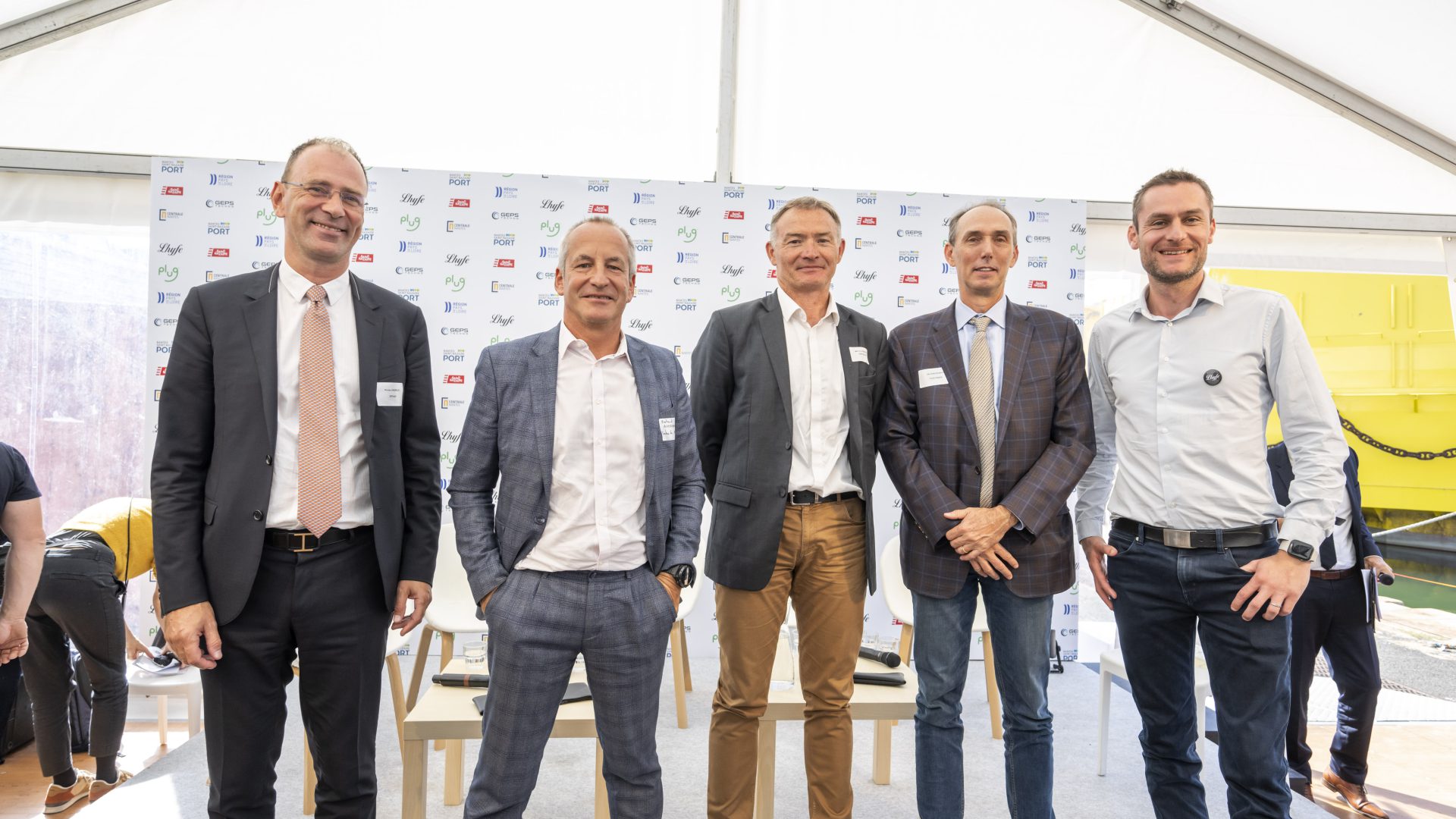
To achieve this technological feat, Lhyfe relied on the facilities of the offshore testing site, SEM-REV, operated by Centrale Nantes. At the end of the quayside test phase, the Sealhyfe platform will integrate the SEM-REV offshore testing area, off the coast of Le Croisic, about 20 kilometres from the coast. The device will then be supplied with electricity by the pioneering floating wind turbine installed within the offshore test site in 2018 and still unique in France today.
The electrolyser was supplied and optimized for these exceptional operating conditions by Plug Power, one of the market leaders that is strongly engaged in the offshore route. Together, Plug and Lhyfe have developed the first electrolyser capable of operating on a floating platform. The project also benefited from the expertise of French offshore and marine renewable energy players: among these, Chantiers de l’Atlantique for enhancing the resilience of the system to environmental stress, ventilation systems and the electrical architecture of the system; Geps Techno and Eiffage Energie Systèmes for the system’s integration on a platform and the naval architecture of the latter; the Port of Saint-Nazaire, and Kraken Subsea Solutions, which participated in the design of the underwater electrical connection to the renewable marine energies produced on the SEM-REV platform.
A first six-month trial phase is being started at quay, in the port of Saint-Nazaire, to obtain initial reference measurements and test all of the systems. At the end of this first stage, Sealhyfe will spend a period of 12 months off the Atlantic coast. It will be installed less than a kilometre from the floating wind turbine, fixed to the ground by a system of anchors and connected to the site’s underwater hub using an umbilical designed and dedicated for this application (energy and data transfer). At the end of this trial, Lhyfe will have a substantial volume of data, which should allow it to design mature offshore production systems, and to deploy robust and proven technologies on a large scale, in keeping with the EU’s objective to produce 10 million tonnes a year of renewable hydrogen by 2030.
Sealhyfe has the capacity to produce up to 400 kg of renewable green hydrogen a day, equivalent to 1MW of power. By 2030-2035, offshore could represent an additional installed capacity of around 3 GW for Lhyfe. “Today our hydrogen is much cheaper than grey hydrogen,” says Créach, “because we have optimized all the different aspects of the production sites and this means that we are able to produce at a good price. From the Lhyfe side, we wanted to prove that green hydrogen is feasible today, we have done it in just one year and half. We don’t have to wait and we should not wait because it’s important to act today. We just need companies that want to push these projects in order to become operational as soon as possible.”
TO READ THE FULL ARTICLE IN THE MAGAZINE CLICK HERE