FPT Industrial F28
This is not Grey’s anatomy, this is the FPT Industrial F28 Diesel-of-the-year-2020’s anatomy! Listen to Umberto Gammieri, our ‘surgeon’, FPT Industrial chief engineer. Fpt Industrial F28: after the genesis, we talk about the ‘organs’ What are the most innovative elements of the F28? The most innovative element is certainly the fact that it has been conceived and […]
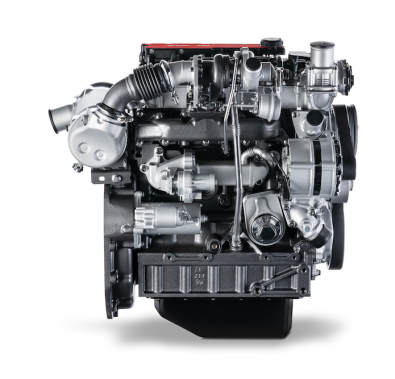
This is not Grey’s anatomy, this is the FPT Industrial F28 Diesel-of-the-year-2020’s anatomy! Listen to Umberto Gammieri, our ‘surgeon’, FPT Industrial chief engineer.
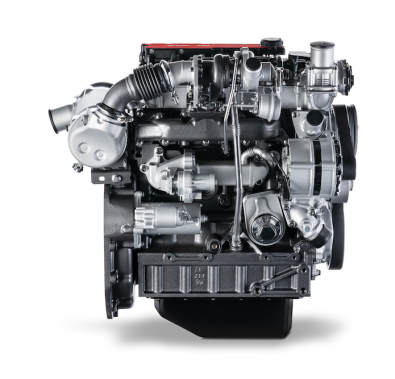
Fpt Industrial F28: after the genesis, we talk about the ‘organs’
What are the most innovative elements of the F28?
The most innovative element is certainly the fact that it has been conceived and designed according to a modular approach, i.e. to be integrated to respond to different needs of use.
The three main pillars are: compactness and performance, multi-fuel, ready-for-electrification. On the diesel core-engine we have worked with a view to high torque delivered at low rpm and small dimensions for installations on compact machinery.
Talking about the gas version, in addition to the concepts of sustainability and enabler for circular economy models of which FPT is a pioneer, the brand has a strong experience in CNG technology (stoichiometric combustion, no EGR, multi-point injection, proprietary combustion control to ensure emissions reduction and performance). Finally, with regard to electrification, the idea is a scalable approach and integrated solution to ensure compactness.
What about the mechanical set-up?
In the F28, everything has been optimised for compactness and performance, for example the crankshaft. Making it in steel allowed us to reach the high combustion pressure targets while maintaining a packaging comparable to a 3-cylinder engine. The camshaft is in the crankcase, like the F5. It has the advantage of keeping the engine lower.
What type of EGR have you adopted?
We use a cooled EGR, conceptually similar to our 3.4 and 3.6 liters diesel engines but with specific layout and integrated path in the head for greater compactness. The question goes into the field of homologation. For powers below 56 kW (NOX 4.7 instead of 0.04), the EGR light is sufficient to handle NOx. In the exhaust manifold there is an additional runner, the fifth, which intercepts the gases before they enter the turbine. Then there is the passage inside the cylinder head, tangent to a water jacket, where the first heat exchange between water and gas takes place, which then enters the EGR valve, on the hot side. Finally in the cooler, where it is further cooled and enters the intake manifold. It has no external pipes, being directly connected to the base.
And the gas version?
We adopt the multipoint injection and confirm the stoichiometric combustion approach. Moreover, it is without EGR. We have revised the upper part of the engine. The head has a specific design, for compatibility with the injection system, with a different swirl level compared to diesel. The exhaust manifold is of a more resistant material, because the exhaust temperatures are higher than diesel. The compression ratio of the gas engine is lower, so both the piston and the combustion chamber are changed, the rings have a specific design to minimize leakage in the chamber. The catalytic converter on the gas is 3-way.
What about the hybrid?
We are working on different electrification solutions, the concept presented at Conexpo foresees a parallel hybrid architecture, in P2 configuration, where the electric machine is mounted on a flywheel, guaranteeing the compactness of the integrated propulsion system. The solution shown is 48V, with continuous electrical power of 20kW (up to 32kW peak), thus allowing the downsizing of 75Kw machines. The model is scalable on future high voltage solutions, to increase the available electric power and evolve towards solutions with a higher level of hybridization. The system uses an integrated pt control architecture. The benefits are: increased efficiency, improved transient performance for e-boost, optimized start-stop management logic, enabler for smart auxiliaries.