John Deere. Engines to Saran
John Deere. In the heart of France, near Orleans, John Deere supplies both Oems and its factories. Within this perimeter every engine paradigm is represented, from stationary to marine applications, from machinery to some agricultural applications. John Deere, industrial engines and Saran is a ‘ménage à trois’ that reached half a century of lifetime. In […]
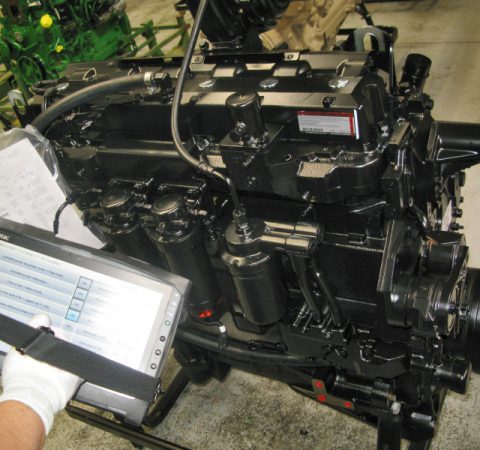
John Deere. In the heart of France, near Orleans, John Deere supplies both Oems and its factories. Within this perimeter every engine paradigm is represented, from stationary to marine applications, from machinery to some agricultural applications.
John Deere, industrial engines and Saran is a ‘ménage à trois’ that reached half a century of lifetime. In 1963 the echo of WWII was fading and post-war France was sitting at the table of the great Powers. Today, the factory numbers tell a story of about a thousand employees, eighty-one dedicated to maintenance, organized on three shifts, half of the production destined to the free market, about 600,000 components handled annually, 1,543 assistance centers, 40 million investment for Tier 4 Final production line.
John Deere. R&D between Saran and Waterloo
The research and development at this site carry out a dual task: the first is a multipurpose one, supporting the Waterloo, Iowa facility, where the R&D Center is located, the second one is focused on Oem applications in the Emea area. John Deere concentrates in Saran most of its ‘customer oriented’ activities, outside the boundaries of Deere machines. Within this perimeter, a production line is dedicated to power generation units customization, redefining the blower and pump layout, cabling, capacity and placement of sup, air compressor alternator and radiators.
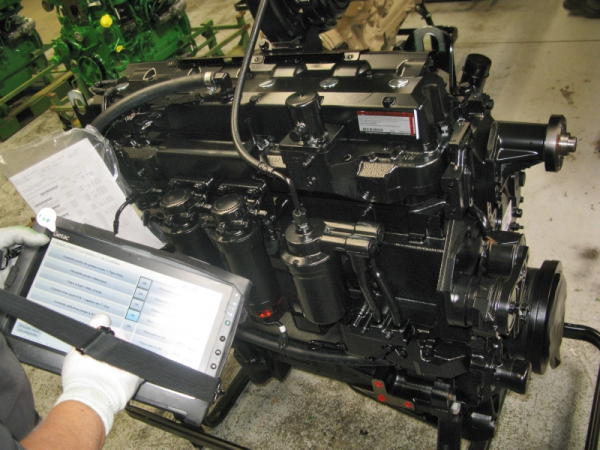
Power generation
John Deere plays heavy trump cards in power generation such as Kohler-Sdmo. Moving from Orleans to sketch John Deere’s production cartography we need to start from Waterloo, the 9 and 13 liters manufacturing site, and cross the Mexican border to Torreon, where 4.5 and 6,8 liters are manufactured. Jumping to Argentina we come to Rosario, where 2.9 to 9 liters engines are assembled. Next step is Asia, featuring two factories focused on their respective reference markets: Pune in the Indian subcontinent for 2.9 liters engines, and Tiangjin in China for 4.5 and 6.8 liters. The assembly line revolution was mentioned speaaking about Tier 4 Final adaptation. The progressive upgrading of production lines and procedures involved four areas: the cylinders block, the 2-valve head line, the four valves head line, the crankshaft. The automation process and the dialogue between operator and software coexist in Saran.
Deere procedures
The badge is an example able to verify the compliance of each step to reduce human error to zero. Overall, there will be over 150 component verification procedures. It is possible to adjust the inclination of the belt during a couple of assembly steps to facilitate ergonomics and operating modes. Alerts also intervene to detect any non-conformity, for example when handling valve guides. Before facing one of the 11 test benches, Deere multi cylinders repeatedly undergo electronics checks. Some operators make use of a tablet: assembly procedure and individual components are displayed so to directly check possible discrepancies, locating the operations to be verified (the oil level rod, for example, is highlighted within a colored rectangle). Checks are updated in real time and draw a compliance curve projected on video. The testing is done both by disassembling the engine block and then processing the individual components or by testing each unit in one of the 11 Avl cells. Among the verification procedures we also find the simulation of camshaft operation and a ‘radiography’ to detect impurities. The final phase, that of painting, makes use of water paints at 80 °C for thirty minutes, allowing the dispersion of VOC.