Kohler: science, not fiction. Interview with Massimiliano Bonanni
Massimiliano Bonanni, General Manager Product Strategy at Kohler Engines, tells us about the nuances of energy at Kohler: ICE, hybrid, hydrogen, electric, alternative fuels considered in the light of the ecosystem context and their plausibility. Read the full article in the May issue of Powertrain International.
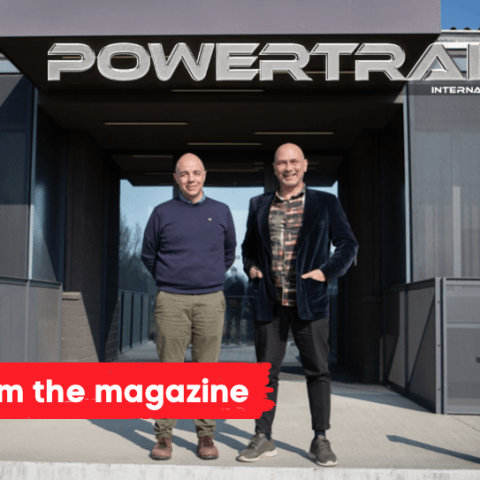
It is a sunny day in Reggio Emilia, an early spring bud anticipating our arrival. What used to be Lombardini has since 2007 become one of the headquarters of Kohler Engines, a company that together with Power Systems, Home Energy, Kohler Uninterruptible Power, Clarke Energy, Curtis Instruments and Heila Technologies forms the Kohler Energy division of Kohler Co. In November, it was announced that by the first half of 2024, Kohler Energy will be majority-owned by the Platinum Equity investment fund; until then, Kohler Co. will operate as a single company. David Kohler will remain on the Board of Directors. From the US, Matthew Louie, CEO of Platinum Equity, sent a clear signal: “We look forward to working with Brian Melka and the management team to continue to invest in the company and maximise its potential”. What potential? We ask Massimiliano Bonanni, General Manager Product Strategy at Kohler Engines. With him, we do not limit ourselves to a didactic product review. We delve into the folds of the energy transition.
“According to Kohler, the future of energy is multidirectional, as there is no single, universal solution. The world will require a plurality of approaches to meet a variety of needs”. And here we go straight to the heart of the matter; an Hamletian doubt, at least for hardcore engine makers. What about the internal combustion engine? “The ICE is not dead and will continue to be one of the pillars of the multi-energy future. Mind you, electrification makes sense and clssaims its place in many contexts. Take for example a car used for short rides. If the owner has photovoltaic systems and a wallbox, then a BEV is the most sensible choice. However, in the case of heavy vehicles, this solution may be more problematic due to the power, time and energy involved in recharging. In my opinion”, Bonanni points out, striking a chord of doubt with a large section of the industry,“there is not enough energy available to convert the entire vehicle fleet to electric. Let’s make a rough estimate to clarify this concept. Given the 40 million vehicles on Italian roads (source: La Stampa, April 4, 2023), let us assume that they are not recharged daily but every five days, assuming they have sufficient autonomy. So, every day, around 8 million cars would need to be connected to the electricity grid. Assuming an average charging time of 20 minutes each, spread out over 24 hours – which implies that someone would have to get up at 2 a.m. to leave the column with their neighbour – this would imply around 100,000 vehicles connected simultaneously to a 250 kW V.3 supercharger. After a quick estimate, this means that – under these conditions – 25 GW of power would be required from the grid. To understand the magnitude of this figure, I will give two examples. A 250-kW V.3 supercharger is equivalent to the power required for more than 80 residential units in an apartment block, each with a standard contract of 3 kW. The 25 GW corresponds to about 20 percent more than the gross installed electrical power in Italy (source: Terna, statistical data as of December 31, 2022). This estimate is an understatement, since, if for any reason the number of simultaneously connected vehicles were to reach 500,000, the required power would instantly increase to 125 GW, which is equal to the gross installed power in Italy. The infrastructure is not a problem, as it can be built, but the real challenge lies in securing an additional energy source. Will it be possible to meet it solely with renewable sources? Maybe yes, maybe no. The challenges of density and recharging time are addressable and solvable. The crucial issue remains the energy source. And this is exactly why, under these conditions, internal combustion engines cannot disappear.” What strategies are realistically at hand? “The solution? Having other alternatives, perhaps less effective but at least more immediate and sustainable, and above all feasible. One solution within reach is HVO, a hydrotreated vegetable oil derived from waste, which does not compete with food crops, as biodiesel does. It has two disadvantages, namely the high cost of production and reduced availability. But it allows a reduction in total CO2 emissions of up to 90 percent. It is 100 percent fossil-free and 100 percent recycled, and can be distributed, managed and stored like any other conventional fuel. HVO requires no investment, neither from the OEM nor the infrastructure. The same advantage also characterises e-fuels, which despite their higher production cost can still contribute to decarbonisation. If our goal is to reduce CO2 emissions, then we must focus on improving the overall efficiency of vehicles. In this context, electrification, understood as hybridisation, plays a crucial role in optimising energy management. On the one hand, it enables the recovery of energy when the engine acts as a brake (e.g., when slowing down), and on the other hand it delegates the management of power peaks to the electric part, thus enabling the endothermic engine to be sized correctly and fuel consumption to be minimised. Before the advent of hybrids, internal combustion engines were sized according to the peak power demand of the application, although this peak could only occur in 1% of the vehicle’s time of use. With today’s hybrid systems, on the other hand, it is possible to size the engine for the basic energy demand, thus reducing specific consumption, and entrust peak power management to the electric component (e-boosting). This is the famous rightsizing”.
The latest frontier in this decarbonisation dilemma is hydrogen, a carbon-free fuel. Kohler places the needs of OEMs at the top of its priorities, working alongside them to find the best possible solution. Among the options under consideration, hydrogen has gained a prominent place.
“At Agritechnica 2023, we presented our KDH engine, a 2.5-litre direct injection engine. Based on the KDI 2504 diesel, we have developed a hydrogen-fuelled combustion system, which maintains the same performance as diesel, thus ensuring the same machine productivity, while at the same time drastically reducing emissions. Our goal is to demonstrate that it is possible to make a transition from diesel to hydrogen without requiring further investment in engine architecture. To date, two key factors have hindered the development of hydrogen as a fuel: the availability of the fuel itself and the infrastructure. The crucial question is: ‘Where do I produce the hydrogen and how do I transport it to the car?’ It is debated whether to produce it on-site or transport it over long distances. In the not-so-distant future, Africa and Arabia could emerge as major sources of hydrogen production. These regions are characterised by abundant sunshine and seawater reserves, which, if desalinated, could be used to produce hydrogen without competing with the extremely limited freshwater resources” (see box on the Gulf-to-Europe hydrogen pipeline project).
“We started our hybridisation journey with a project called K-HEM, which stands for Kohler Hybrid Energy Module, by applying an electric motor with an oil pump arrangement to a 19kW diesel engine. We wanted to demonstrate the ‘e-boost’ effect, i.e. how much you can increase the performance of a 19kW engine. We achieved 33 kW and 165 Nm peak. Next, we presented the 56kW K-HEM by installing an electric motor on the KDI engine, reaching a peak of 90 kW and over 500 Nm. Finally, we also launched the P2 parallel hybrid version, with a clutch that allows three operating modes: thermal coupled to electric for the e-boost effect; internal combustion only; and fully electric. Among its various applications there are tractors used in greenhouses and forklifts moving between yards and covered warehouses.”
So, what is Kohler’s formula?
“Kohler’s solution is agnostic. We want to be part of the differentiating criteria for OEMs. Kohler is the ideal development partner for OEMs because we do not impose a technical solution, but we are ready to support them whatever choice they make. We recognise that the future will be characterised by energy diversification, so we are ready to offer a wide range of solutions to meet future customer needs. Internal combustion engines will continue to be part of these solutions, whether they are powered by alternative fuels, such as HVO or hydrogen, or integrated into hybrid systems”.
To read the full story, click here or download the pdf