Perkins CMET can cut OEM time to market by up to nine months
Perkins CMET, or rather Customer Machine Engineering Team, includes individuals with a vast experience of Perkins products and the specialised skills needed to take a project from concept to either a prototype/production machine or a functional, fully tested machine depending on the need. The team includes engineers, technicians and business specialists organised to work in […]
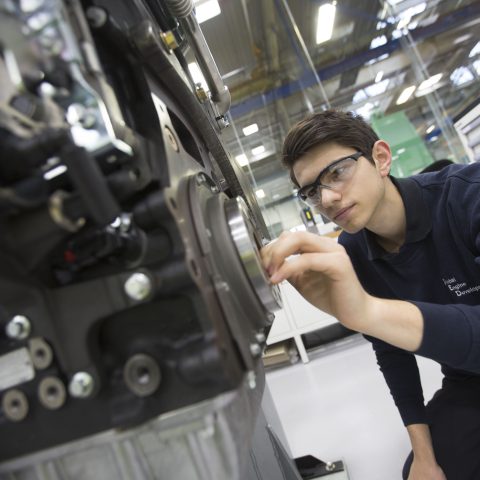
Perkins CMET, or rather Customer Machine Engineering Team, includes individuals with a vast experience of Perkins products and the specialised skills needed to take a project from concept to either a prototype/production machine or a functional, fully tested machine depending on the need. The team includes engineers, technicians and business specialists organised to work in close collaboration with customer engineering and business teams to achieve optimised results in minimum time.
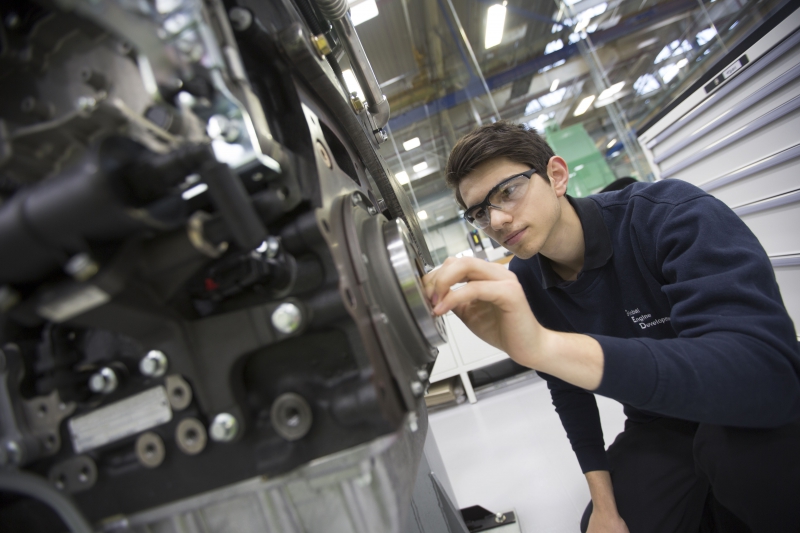
Perkins CMET teams (and benefits for users)
OEMs can turn to Perkins CMET whenever they need to create an upgraded or new product. In such cases, OEMs have to make a fundamental choice. Either spend time and resources creating an internal team to research and develop a solution from scratch, or take advantage of hundreds of years’ worth of real-world, hands-on experience that already exists.
Since 2017, Perkins CMET collaborations have helped customers cut as much as nine months from R&D programmes to upgrade existing machines or develop entirely new products. In particular, the CMET team includes an engineering lead and a sales lead to facilitate effective communication and coordination between Perkins and the customer to drive the CMET process through to completion; design engineers responsible for the design of the new engine installation and creation of engineering drawings; a supply network specialist to source, purchase and deliver components and organisation of the customer machine.
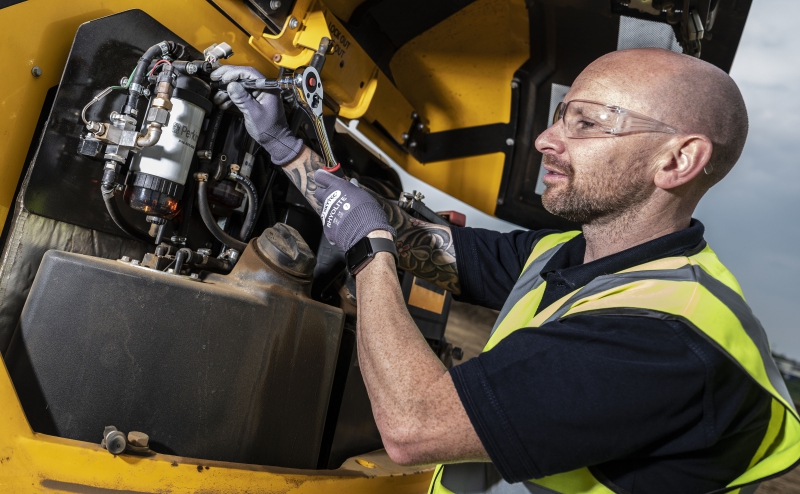
Meeting emissions standards or updating existing machines
Also, testing and development engineers and technicians are required to instrument and baseline test original machine; strip, rebuild and instrument machine with new engine; test and develop new engine installation and finally re-baseline test new installation.
By collaborating with Perkins CMET, OEMs can access a unique pool of real-world experience to help them deal with challenges, such as meeting emission standards (the EU Stage V is a valuable example), updating existing machine or installing Perkins in place of a competitor engine.
In short, OEMs can choose to reinvent the wheel every time they upgrade an existing product or develop a new one or an OEM can take advantage of Perkins CMET to achieve its goals an average of nine months faster and at a lower cost, and potentially beat its competitors to market.