Agritechnica/Systems & Components 2023: hydrogen makes off-highway machinery drive systems green
Combustion engines and fuel cells, running on climate-neutral hydrogen, can be used to power off-highway vehicles – at Systems & Components 2023 running parallel to Agritechnica 12-18 November, Hanover, Germany.
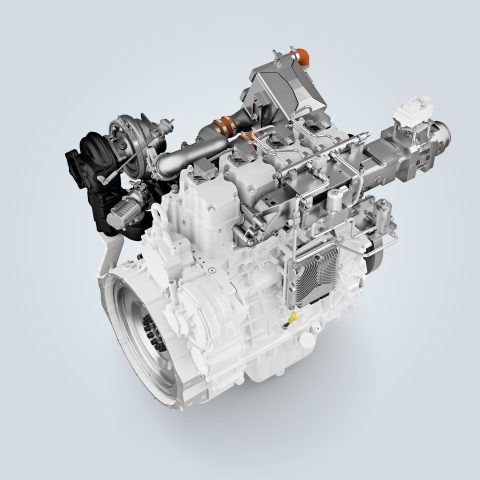
Combustion engines and fuel cells, running on climate-neutral hydrogen, can be used to power off-highway vehicles – at Systems & Components 2023 running parallel to Agritechnica 12-18 November, Hanover, Germany.
The Systems & Components event in Hanover, Germany, will be offering practical solutions for hydrogen-powered combustion engine and fuel cell technologies that can be used alongside electric drives in various hybrid configurations to power off-highway vehicles.
From 12 to 18 November, the B2B marketplace that will be taking place as part of Agritechnica, the world’s leading agricultural machinery exhibition, will be offering developers and design engineers an information and discussion platform around the latest developments and alternative fuels. There visitors can see what an “ideal” drivetrain for a hydrogen-powered excavator or tractor might look like.
Modern hydrogen engines, like those that will be presented at Systems & Components in mid-November, are based on familiar and proven combustion technology, adapted for a sustainable future. The advantages of this strategy are readily apparent: a hydrogen combustion engine can be installed in the same machine as a diesel engine using the same gearbox, cooling system and hydraulic system. The engine can operate in dusty environments, is able to withstand severe vibrations and is available in all sizes and configurations. For the switch to hydrogen-powered drivetrains, vehicle manufacturers and fleet operators can stay with a familiar architecture in which a piston engine is powered using hydrogen rather than diesel, petrol or natural gas.
Proven basis, sustainable fuel
In contrast to the fuel cell, the hydrogen combustion engine is an inexpensive alternative that can be quickly implemented using the present manufacturing infrastructure, achieving zero carbon mobility in agriculture and construction. While its efficiency is lower than that of the fuel cell at low and medium loads, it is higher at full load. Because of this, experts, such as Thomas Pauer, President of the Bosch Powertrain Solutions division, regard the hydrogen engine as a gateway technology for off-highway markets and a complement to fuel cell technology, which is rapidly reaching its limits in the heavy-duty and off-road sectors. “Construction machinery often operates at rest under high loads, which is precisely where the hydrogen engine stands out with its high efficiency and robustness,” emphasises Pauer. An example of this concept is the TCG 7.8 H2 from Deutz (below), a six-cylinder engine, based on an existing modular engine system and suitable for off-highway use. It emits no carbon and delivers an output of 220 kilowatts. As well as its pilot application in a genset (a combined engine and generator) for producing electricity, the engine will be demonstrating its abilities in an 18-tonne truck, as part of of the HyCET project. Deutz is already planning to start mass production of the engine in 2024.
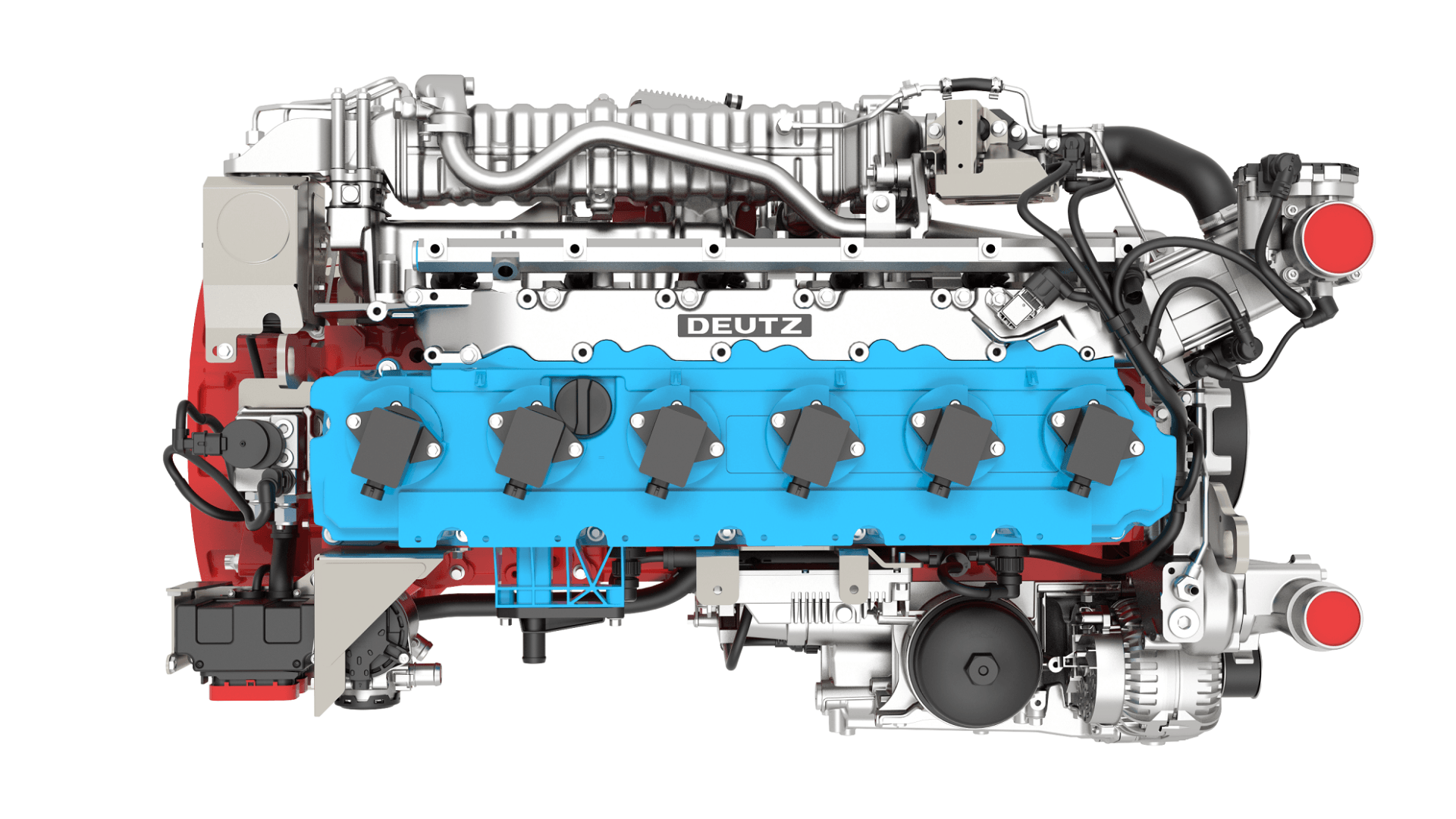
“The use of hydrogen can quickly make numerous heavy-duty and off-road applications climate-neutral,” confirms Peter Wieske, Director Corporate Advanced Engineering at Mahle. Nevertheless, the prevention of engine knocking and premature ignition while maintaining the compression ratio, engine efficiency and output yield, is challenging. In this, the pre-chamber ignition, developed by Mahle Powertrain for Liebherr Machines Bulle, plays a crucial role. In order to achieve stable operation without knocking despite high compression, hydrogen engines must run with excess air, such that a conventional spark plug is incapable of igniting the mixture.
Pre-chamber technology for stable combustion
Mahle Jet Ignition (MJI) solves this problem by igniting a small quantity of a flammable mixture in a cylinder pre-chamber. The resulting gas plasma is routed through small openings into the main combustion chamber where, thanks to its high energy content, it quickly and uniformly ignites the main gas mixture. According to the company, tests with Liebherr’s H966 and H964 engines have shown outstanding results in terms of combustion speed, output and emissions. The H966 is the core element of Liebherr’s new crawler excavator, the R9XX H2. This uses a hydrogen engine that was developed for field tests and is based on port fuel injection (PFI). The results achieved with this technology show the potential of the hydrogen drive for off-highway applications. Liebherr is also working on further hydrogen-based drive technologies such as H2 direct injection (DI). The latter promises a higher power density than H2 port fuel injection and is therefore suitable for demanding heavy-duty applications in the construction and mining industries. Bosch is also working on systems with port or direct fuel injection and is involved in more than 100 projects worldwide. As well as direct injection of hydrogen, the new AFI-LP injector (alternative fuel injector – low pressure) can also use other fuels such as methanol, thereby ensuring the greatest possible flexibility for engine manufacturers.
Liebherr aims to start mass production of its hydrogen engines by 2025. Just like Bosch, the technology company is also conducting research on injection solutions in order to further optimise combustion and the power density. “Our engineering team’s expert knowledge of alternative fuels is of central importance in this development,” explains Bouzid Seba, Head of Advanced Development at Liebherr Machines Bulle. His statement underscores the open-technology approach that Liebherr is taking in dealing with various technologies and the fuels that are suitable for them. Besides hydrogen-powered engines, several research projects are currently being conducted into alternative fuels. One example of this is a dual-fuel engine that can run on hydrogen and HVO (hydrotreated vegetable oil) or with just HVO. Many of the diesel engines on show at Systems & Components are now fully compatible with renewable HVO fuels, which is already bringing them close to the zero-carbon target.
Rethinking engine power
These activities show that alternative fuels require optimised engines, designed for compatibility from the ground up, and Cummins is working on such new engine platforms. “The goal is to achieve a more efficient engine with a higher power density by implementing flexible overhead camshaft systems, improved cooling and reduced friction. We have also developed an advanced, optimised combustion chamber for the fuel mixture,” says Srikanth Padmanabhan, President of the Engine Business, Cummins. The objective here, too, is to avoid output limitations and other compromises related to switching current diesel or natural gas engines over to hydrogen.
One of the as-yet unsolved problems is the tank capacity, as hydrogen takes up a significantly higher volume than diesel for the same energy content – around five to eight times the tank volume. Stable carbon fibre pressure vessels are a possible approach to providing larger volumes of hydrogen for a fuel cell or a combustion engine. However, pragmatic solutions are also being developed, such as a mobile refuelling unit from JCB. The British construction and agricultural machinery manufacturer has invested over 100 million pounds in developing highly efficient hydrogen engines and has already presented functioning prototypes of an excavator and a telescopic loader. These are now being supplemented by a mobile filling station, which enables the machines to be refuelled quickly and easily on site using a nozzle. The process is the same as that used on construction sites, where conventionally driven machinery is refuelled with diesel from a tanker truck.
The hydrogen future is set to start in Hanover
The technological potential of hydrogen in agriculture and forestry will also be under discussion at Systems & Components. While electric vehicles are conquering the roads, the capacity of battery-powered vehicles, except for some compact machines with outputs of less than 50 kilowatts, is often insufficient for field use. Walter Wagner, Research & Development Director at AGCO/Fendt, states “Compared to conventional energy sources, electromobility is not an option for high output machinery. We are conducting research into alternative solutions, such as the use of hydrogen.” In such applications, the fuel cell stack comes into focus as an additional drive variant. It converts chemical energy from hydrogen and oxygen directly into electrical energy, which is then used to drive the motors or be stored in buffer batteries. Fuel cells must be precisely controlled and monitored. The volume, humidity and cleanliness of the input air are equally as important as the temperature of the hydrogen that is supplied. The exhibitors at Systems & Components will be offering all of the components required to control and monitor fuel cells and continue to develop them further.
Researching hydrogen infrastructure for agricultural use, the collaborative H2Agrar pilot project, in which Fendt is taking part, received the “DLG Agrifuture Concept Award” in 2022. For the first time, tractor prototypes, powered by a hydrogen fuel cell, will be employed, delivered by Fendt to farms in Haren in Lower Saxony’s Emsland region in Germany earlier this April. These will be operated under real conditions throughout the entire project period. In parallel, research is being conducted into the technical requirements for a suitable hydrogen infrastructure for the agricultural sector. Looking ahead to this year’s Systems & Components, many approaches for achieving a climate-neutral powertrain will be on show from 12 to 18 November at the trade fair grounds in Hanover. The search for high-performance solutions to decarbonising mobile machinery is well underway, including the development of carbon-neutral combustion engines, using hydrogen or synthetic fuels, as well as electric drive trains.
Opening image: Liebherr presents its 4-cylinder engine H964 equipped with DI technology