Brokk, the demolition robot with electric (or diesel) soul
The Brokk 900 is available both with a 71-kilowatt ABB electric motor and in the diesel version (with Kohler or Kubota engines), with emissions standards up to Tier 4 Final for the American market or Stage V for the European market. The power supplied is in any case around 55 kilowatts.
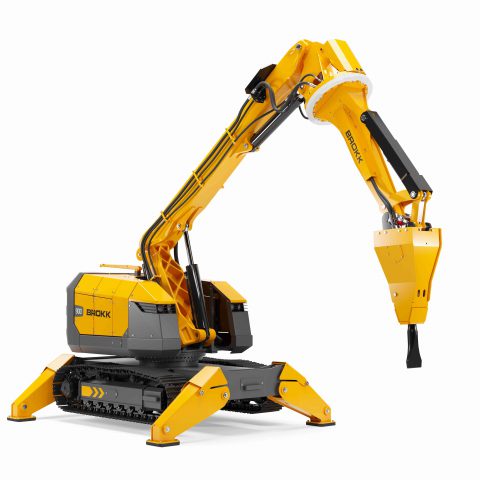
Brokk demolition robots were born electric, although some models are also provided with a diesel engine, Stage IIIA or Stage V according to the specific requirements of the countries they are addressed to. The full article of our latest Fish-Eye is available here, page 28.
Demolition robots vaguely resemble excavators, although they do not have a cabin or controls that can accommodate the operator. The remote-control system makes it possible to work in environments that are particularly dangerous or even inaccessible to humans, so the robot is in some cases the only possible solution.
So, who are the typical users of these machines? «Users who need to work in very confined environments, mainly inside factories, civil buildings, tunnels, microtunnels or confined environments where humans must absolutely stay at a safe distance», explains Carlo Montorfano, Sales Manager at Brokk Italy. «In the industrial field, Brokk machines are required in metalworking: steel, aluminum, copper, zinc, lead foundries. Here they work in furnaces for the renovation of refractory materials or in the cleaning of casting slags, for example. All environments characterized by high temperatures and requiring high productivity in high-risk situations for the operator».
Brokk demolition robot available in two options
A varied range, that of Brokk demolition crawlers, which starts from a model weighing 600 kilos and 60 centimeters wide. This reaches the mini excavator segment, with the advantage of guaranteeing a level of productivity – in terms of power supplied to the arm – comparable to much heavier and bulky machines. At the top of the range we find the Brokk 900 weighing 11.5 tons and 2.15 meters wide; evolution of the 11-ton Brokk 800, the new machine has made important progress in terms of design, power (as for the engines, of course, we will talk about it in the box above), operation and penetration capacity of the hydraulic breaker. Without significantly increasing size and weight.
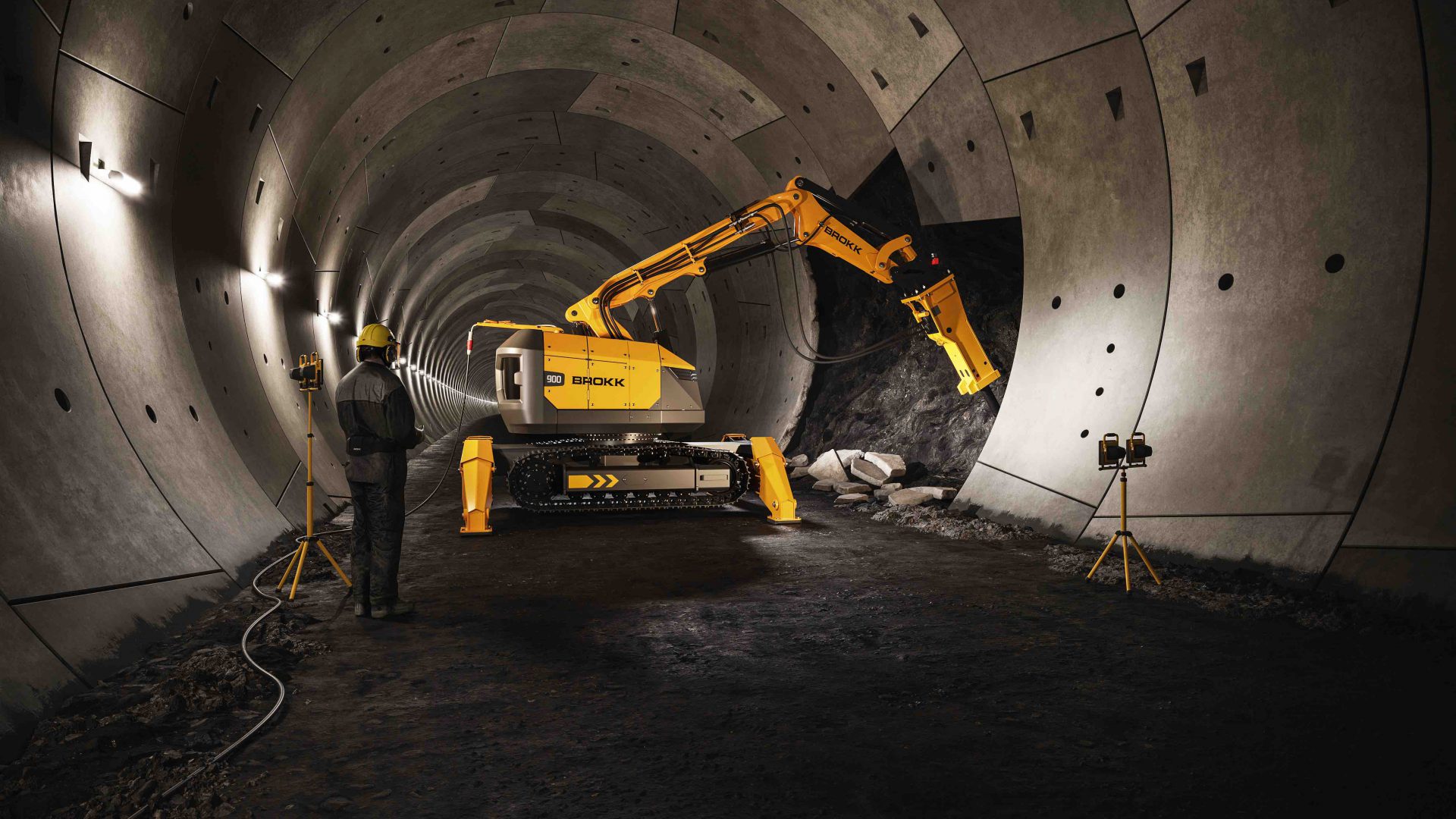
Two options are available: standard with heavier and more powerful hydraulic hammer and the Rotoboom version with 10-meter range high-precision rotating arm system. Brokk machines are produced in-line at the Swedish plant following strong research development. In addition to the need to make the machines absolutely heavy-duty to maximize reliability and durability, in some sectors there is a high need for customization in order to protect the machines, and especially the most delicate parts, from very high temperatures, collapses or even from any overturning of the robots themselves.
71-kilowatt ABB electric motor
The Brokk 900 is available both with a 71-kilowatt ABB electric motor and in the diesel version (with Kohler or Kubota engines), with emissions standards up to Tier 4 Final for the American market or Stage V for the European market. The power supplied is in any case around 55 kilowatts. «We can say that the Brokk machines were born electric, precisely because for the most part they are used in closed spaces where an electric motor, therefore without emissions, is a great advantage. Some models, including the 800 before and now the 900, also provide the diesel option for environments characterized by long distances, where managing an electrical cable generates major problems», explains the sales manager of Brokk Italy. Currently, there are no batteries capable of supporting the Brokk machines and above all of powering extremely heavy tools such as hammers, cutters or drills. While waiting for a still hazy future regarding the