JCB: hydrogen engine debuts at the ConExpo
JCB’S £100 million project to produce super-efficient hydrogen engines was given its international debut a few days ago at ConExpo
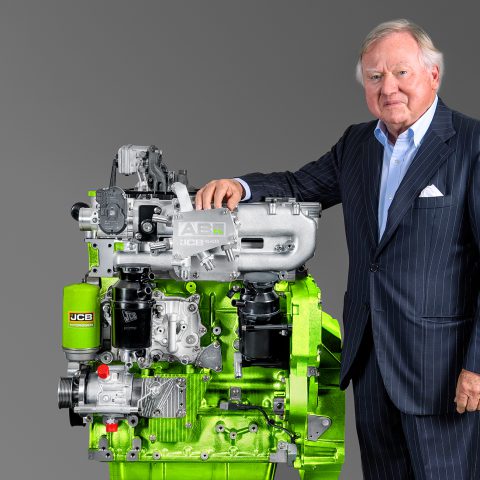
JCB ’S £100 million project to produce super-efficient hydrogen engines was given its international debut a few days ago at ConExpo, one of the world’s biggest construction equipment fairs.
A team of 150 engineers is working on the pioneering initiative to develop hydrogen combustion engines – more than 50 prototypes have already been manufactured at JCB’s UK engine plant.
The wraps came off the brand-new JCB hydrogen combustion engine – the company’s zero-carbon emissions solution for construction and agricultural equipment at the ConExpo 2023 show in Las Vegas as part of the International Fluid Power Exposition (IFPE).
JCB Chairman Anthony Bamford is leading the project to develop JCB’s hydrogen technology. Lord Bamford said: “The JCB engineering team has made enormous strides in a short space of time to develop a hydrogen internal combustion engine. As the first construction equipment company to develop a fully working combustion engine fueled by hydrogen, I’m delighted we are now able to present this technology on the international stage.”
Prototype JCB hydrogen engines are already powering backhoe loader and Loadall telescopic handler machines. JCB has also made a major breakthrough in proving the wider appeal of hydrogen combustion technology by installing one of the super-efficient hydrogen engines into a 7.5-ton Mercedes truck, a retrofit which was completed in just days. JCB has also unveiled its very own designed-and-built mobile refueller to take the fuel to the machines. The unit has enough hydrogen gas to fill 16 hydrogen backhoe loaders and can be transported either on the back of a modified JCB Fastrac tractor or on a trailer.
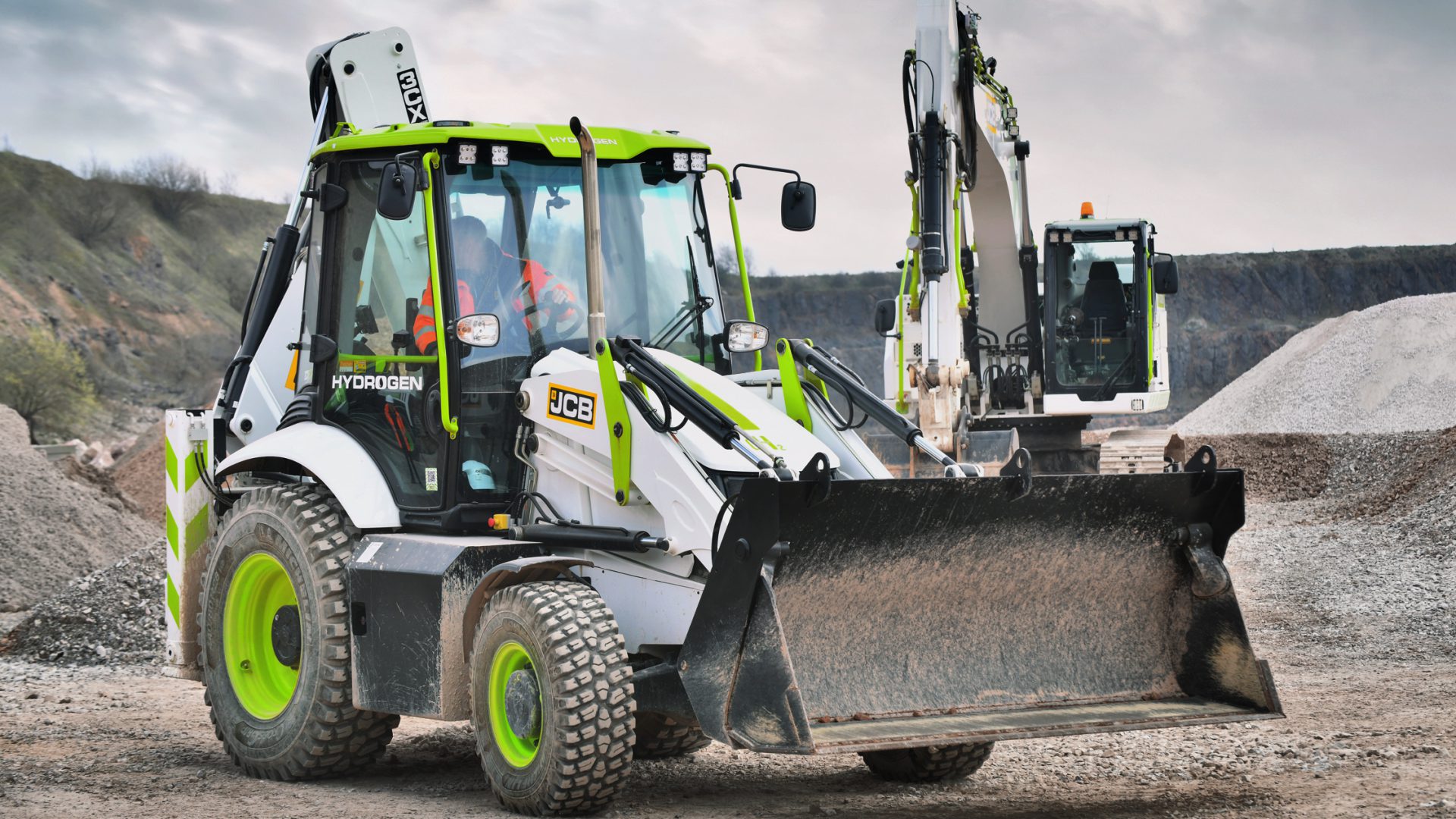
Lord Bamford said: “The JCB engineering team has gone back to first principles to completely re-design the combustion process to work for hydrogen. In doing so, they have achieved two major things: secured JCB’s place in history as the first construction equipment company to develop a fully working combustion engine fuelled by hydrogen and steered us toward the production of a landmark 50 hydrogen combustion engines.”
JCB and hydrogen: committed to sustainability
JCB’s commitment to reducing emissions goes back almost 25 years, and the latest diesel engines designed to comply with European Stage V regulations have already delivered a 97% reduction in NOx emissions since 1999 and a 98% reduction in particulates. In addition, JCB’s drive to reduce fuel consumption means today’s JCB machines use 50% less fuel on average than those manufactured more than a decade ago. This has saved 16 billion liters of fuel – equivalent to 53 million tons of CO2.
JCB has also been at the forefront of electric technology development to meet customers’ demands for zero-carbon products. While battery electric is suitable for smaller machines which do fewer hours and typically use less fuel, larger machines have a higher energy requirement. This would result in larger batteries which would take longer to charge, making them less suitable for machines that work multiple daily shifts and do not have the available downtime to recharge.
As a result, JCB has concentrated its development of electric machines on its compact range, including the 525-60E Loadall telehandler and the 19C-1E mini excavator – the world’s first electric mini excavator. As the company examines future fuels which deliver zero emissions, it has left no stone unturned. In its search for a mobile fuel which can be taken to the machine, ensuring maximum uptime and fast refuelling, HVO, biogas, E-fuels, ammonia and hydrogen have all come under the microscope. Interestingly, JCB engines have been approved for use with HVO since Tier 4i engine legislation came into force.
Lord Bamford said: “The majority of these alternative fuels require the production of hydrogen to make, so it makes perfect sense to use hydrogen in the first place because it is a clean zero-carbon fuel which can be produced from renewable energy. Hydrogen also offers a potential solution to the challenge of batteries on larger machines; it allows for fast refuelling and is a mobile fuel solution, allowing fuel to be taken to the machine.”
As part of its hydrogen development, JCB also investigated its use in fuel cells, and in July 2020, unveiled the construction industry’s first-ever hydrogen-powered excavator, a 20-ton 220X.
For the time being, JCB has come to the conclusion that fuel cells are too expensive, too complicated and not robust enough for construction and agricultural equipment. In challenging the JCB engineering team to think differently using technology that is around us in a zero-carbon way, the JCB hydrogen engine was born.
Lord Bamford said: “The unique combustion properties of hydrogen enable the hydrogen engine to deliver the same power, torque and efficiency that powers JCB machines today, but in a zero-carbon way. Hydrogen combustion engines also offer other significant benefits. By leveraging diesel engine technology and components, they do not require rare earth elements and critically, combustion technology is already well proven on construction and agricultural equipment. It is a technology which is cost-effective, robust, reliable and well-known throughout not just the construction and agricultural industry, but the whole world.”