Training center at the FPT Industrial’s Academy
At FPT Industrial's Academy, in its Italian headquarters, Turin, we experienced an example of the training center's theory and practice training
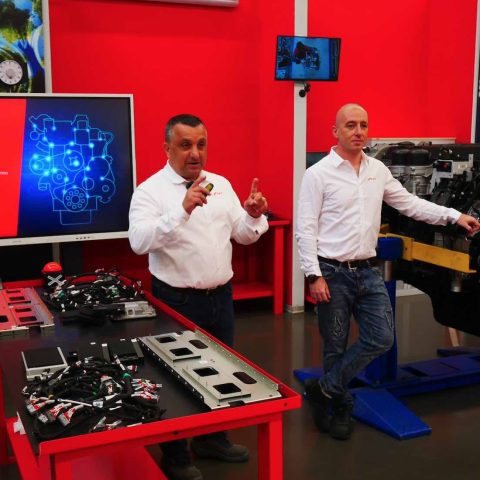
We address the fundamental question of training at FPT Industrial’s Academy, in Turin. Yes, we specify the location, because there are others, organized by geographic macro-areas, in APAC, in Shanghai, in North America, in York, Pensylvania, and in Brazil, for LATAM, in the Sete Lagoas facility. The Indian center, in Pune, is being set up, while in Japan there is a similar structure within the Fuso plant. About customer service we have had the opportunity to talk in the past with Sergio Carpentiere, Vice President – Customer Service and Digital.
FPT has designed the Academy as a place for training, both both in theory and hands-on
Here, at the Training Center, we “get our hands dirty.” With engine oil and more. It would be interesting to dwell on the procedures for disassembly and reassembly of engines and battery packs, but we defer this part to the in-depth discussion in the next issues of POWERTRAIN International. Let us keep to general information. Customer services are the tool kit for customers for everything related to protection, reliability, uptime. Not too far from Turin, in the FPT Industrial France plant, they handle remanufacturing, with replacement entrusted strictly to original spare parts. From the control room at the Italian headquarters, however, they are able to control more than 300 thousand connected engines. The acronym RAS stands for remote assistance: through the app and the engine code, remote connection is allowed and continuity of work, while waiting for the scheduling of of the diagnostic procedure, when it does not even come to the resolution of the faults.
Let us tell you about the Technical Academy
The room where theoretical training takes place is equipped with multimedia whiteboard, projector and an automatic tracking camera with artificial intelligence, which is used for online courses. In the ‘workshop, technicians taking the training courses put their hands on the engines, doing diagnostic exercises and dealing with assembly and reassembly. The activities are divided into four main categories, depending on the audience. There are courses dedicated to the service network, to whom they provide both basic and advanced courses, refresher courses on new engines and new approvals, focus on specific applications. There are lessons for direct customers, who are divided into two groups, for first those with a warranty and post-warranty service network. Very advanced courses are addressed to them, so that the recipients are able to repair, service and maintain FPT engines and powertrains. The other group is made up of those who employ the FPT network for service. These are more essential courses, for general knowledge of the engine architecture and for the work scheduled by the maintenance plan. Internal colleagues have more advanced knowledge of technologies and undergo continuous refresher sessions on approvals, powertrain systems, and various applications. Finally, there are certification courses to the service network, divided into five levels of certification, so that technicians meet certain quality standards, from level zero to the master level, so-called trouble shooting, where troubleshooting and problem solving methodologies are learned.

Differences and similarities among training centers
In the EMEA region, FPT Industrial has 300 technicians in certification to whom they deliver both in-person and streaming and self-paced courses through the LMS platform. For network certification, there is a method of tracking the level of certification attainment, identical to that used for Teardown in FPT’s Academy. A dashboard displays the progress of technicians. The certifications are different in the various training centers because they are designed according to the needs of local customers. For EMEA, where different applications are involved, master courses have been developed, specific to individual applications. In North America, on the other hand, there is strong demand for training on marine engines. In the EMEA area, where 16 dealerships are located in Europe and 5 in the Middle East and Africa, each certification user can access up to 42 modules. Each dealer has a set of workshops for its own geographic area. The module achievement rate, based on the level of technician learning, of each dealership is displayed. Currently the two extreme levels, i.e., zero and trouble shooting have lower percentages than the other two intermediate levels because they were introduced earlier this year.
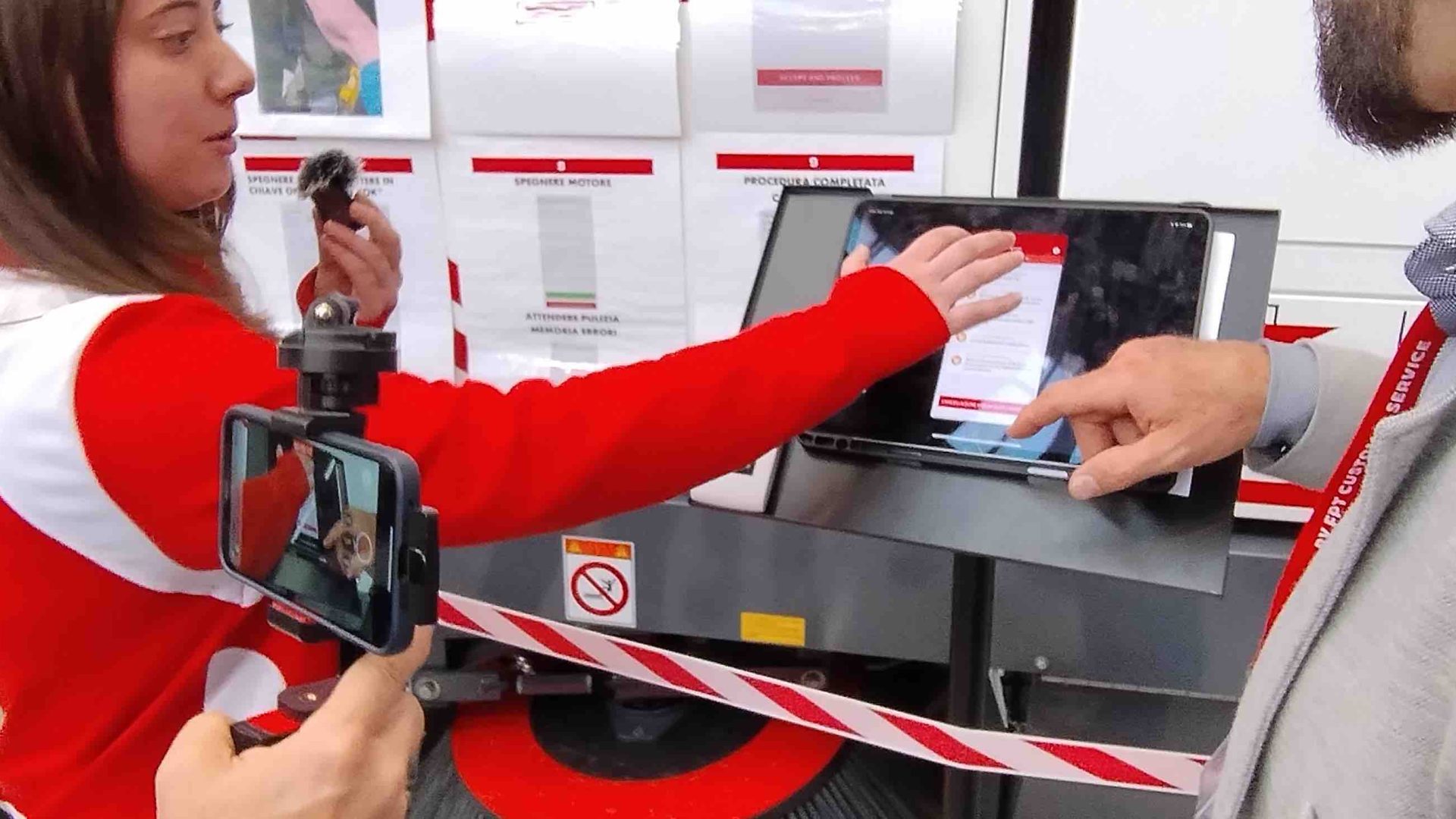