Agritechnica 2023: alternative drive systems for tractors
Agritechnica 2023 (12-18 November, Hanover, Germany) will present state-of-the-art alternative drive systems for agricultural machinery. At the exhibition grounds, for the first time, selected exhibitors will be presenting alternative drive systems in the exclusive Drive Experience outdoor area.
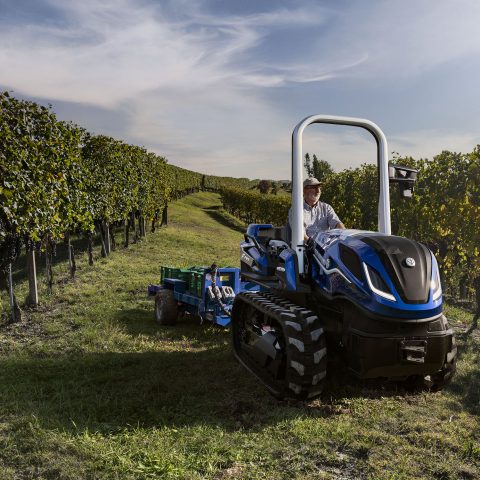
Agritechnica 2023 (12-18 November, Hanover, Germany) will present state-of-the-art alternative drive systems for agricultural machinery. At the exhibition grounds, for the first time, selected exhibitors will be presenting alternative drive systems in the exclusive Drive Experience outdoor area.
Electrical and hydrogen powertrains are just a few of the alternative drive systems finding their place in modern farming. One important reason for the increased interest in alternative drives and fuels is the push to significantly reduce greenhouse gases. To achieve the goals of the Paris climate agreement, CO2 emissions must be reduced quickly and drastically.
Diesel has traditionally been the energy supply of choice for agricultural machinery – with the associated harmful environmental effects. However, greenhouse gas emissions from machinery cannot be sufficiently reduced by improvements to conventional drive technology alone. The transition from fossil fuels to renewable fuels is imperative.
Hydrogen
Hydrogen is a possible substitute for diesel for agricultural vehicles. As hydrogen is carbon-free, its use does not produce any climate-damaging CO2 emissions. However, as its production is energy intensive, a prerequisite for its meaningful use is that this energy comes from renewable sources.
The use of hydrogen in a fuel cell is a special form of electric drive. In contrast to a conventional electric drive where the battery is charged from external sources, the electrical energy to move the vehicle is generated by the fuel cell. Several concept tractors have been presented with fuel cells as their main power source over the years, but none have yet made it into commercial use.
Several important factors stand in the way of fuel cells in agriculture: firstly, there is the challenge of getting enough energy into a standard tractor. The compressed hydrogen pressure vessels need significant space. Using current solutions, a tractor cannot operate at full load for several hours. Additionally, a fuel cell drive requires components that take up space, such as the cooling system, inverter and buffer battery. The latter is needed to support the relatively slow and unresponsive fuel cell. Additionally, a network of hydrogen refueling stations must be created, geared to agriculture. Last but not least, the manufacturing costs for the entire system are still very high.
Methane
Methane is another gaseous fuel that is the focus of attention, as no more greenhouse gases are released during burning as were used during plant growth. The goal is to make the entire process chain and its production CO2-neutral.
Methane can be part of the solution for agriculture. Raw biogas, produced in biogas plants, cannot be used directly as a fuel but must first be desulfurized and the CO2 scrubbed from the methane. The final product is close to pure methane, which is then liquefied or compressed.
Today, liquefied methane, usually referred to as “liquefied natural gas” (LNG), is not particularly suitable for use in agricultural machinery. Despite its relatively high energy density, it has several disadvantages, including the technically demanding and energy-intensive liquefaction process and possible methane emissions during longer idle times and at higher temperatures. Compressed methane, also known as “compressed natural gas” (CNG), is more practical but it has a significantly lower energy densitythan diesel or LNG. This results in larger additional tanks, as well as a shorter range due to limited storage capacity.
A production tractor, running entirely on methane, already exists. The methane, in the form of CNG, is injected into the intake manifold of the 6-cylinder piston engine with 180 hp. The exhaust gas only needs to be treated using a three-way catalytic converter. Technologies such as exhaust gas recirculation, particulate filters or SCR catalytic converters with a reductant, such as AdBlue, are not required. The manufacturer has also presented a preproduction model with a 270 hp engine powered by LNG.
Biofuels
Engine solutions using biofuels like rapeseed oil or rapeseed methyl ester have been around for decades. They can serve as a bridging technology. With an energy density of 93 percent relative to diesel, rapeseed oil is an interesting fossil free alternative.
Rapeseed has the advantage of being widely grown. Any rapeseed-producing farm could use the extracted oil as fuel, while the rapeseed cake produced as a by-product provides a protein-rich feed.
To use rapeseed oil and other biofuels, tractor drive systems must be adapted in terms of engine power and lubrication and other characteristics. A multi-fuel tractor announced by one manufacturer, which can use not only diesel but also biodiesel, vegetable oils and mixtures of these biofuels, has not yet made it to the market.
Battery
At first glance a seemingly innovative technology, electrically powered agricultural machinery is historically nothing new. The first cable or battery powered solutions were already available in the 19th century, but they all lost out to the internal combustion engine.
The passenger car sector is now once again focusing attention on agricultural machinery with electric drive, in which the combustion engine is replaced by one or more electric motors. An electric drive has a lower weight and a smaller installation space than an internal combustion engine. In addition, it is emission-free, generates significantly less waste heat and operates almost silently.
However, the major weakness of an all-electric system is the low energy density of the batteries, which results in high battery weights and volumes as power requirements increase. This is not yet a problem for smaller tractors with moderate power requirements for use on the farm, for grassland maintenance or in the municipal sector. These can simply be charged on the farm or building yard when not in use. The situation is, however, quite different for tractors with high outputs and long operating times. Were one to use current technology for larger tractors, the batteries required would simply be too heavy – 25 tons for a large tractor with articulated steering – with long charging times. Both factors make batteries impractical for field use today.
A revolutionary swarm concept for large machines has been developed by a well-known agricultural machinery manufacturer, in which multiple drone tractors pull the attachments, with the power supplied by cable from the edge of the field via a cable tower connection system. The power distribution vehicle is rated for a total of 1,000 kilowatts. However, such a concept requires major advances with a suitable design.
Solar
Solar-powered sowing and hoeing robots already exist. The GPS-controlled agricultural robots can be used as autonomous machines for very light work with low power requirements in root crop and vegetable cultivation. They are battery-powered, with the required electricity produced by solar cells located on the machine. Solar energy is used to recharge the batteries, allowing the machines to work continuously throughout the day. However, solar drives are not suitable for larger field machines due to the large module areas required.