The importance of battery packs for truck electrification
Research on truck electrification (here, our post about the introduction of the Nikola Tre, at the end of last year) has made significant progress in recent years and the still high level of the prices is expected to decrease in the coming years. Among the primary elements in this research work are the lithium-ion battery […]
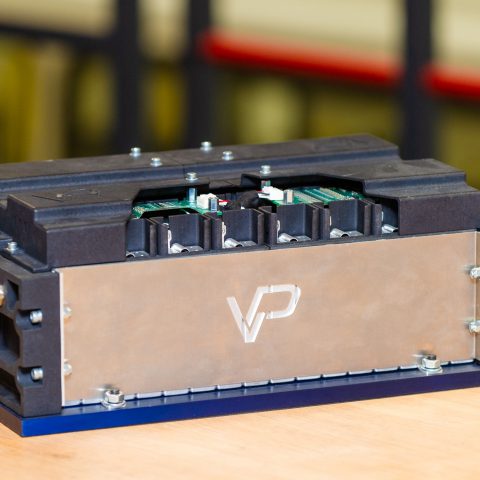
Research on truck electrification (here, our post about the introduction of the Nikola Tre, at the end of last year) has made significant progress in recent years and the still high level of the prices is expected to decrease in the coming years. Among the primary elements in this research work are the lithium-ion battery packs, which stand out as the most critical piece of the puzzle and represent the biggest hurdle before mass adoption can take place.
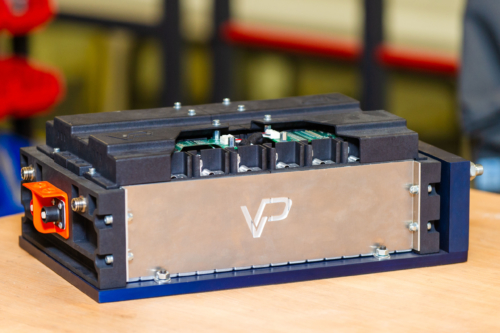
Alexander Schey, the Chief Commercial Officer for Electrification at Allison, and also the former CEO and co-founder of Vantage Power – a company acquired by Allison in April 2019 and specializing in battery pack technology, vehicle integration and connectivity, said something relevant about this topic.
A future with widespread truck electrification
«The primary barrier to widespread e-truck adoption is the cost of the battery pack, which typically is the most expensive system in the vehicle and may represent over 50 percent of a vehicle’s value. Many factors contribute to the cost of a battery pack, and here we discuss three of the most critical; cell cost, pack cost, and if/when the pack needs replacing. Fantastic improvements have been made in the cost of cells. Looking at the cell chemistry most likely to power the e-trucks of the future – lithium ion manganese cobalt oxide (NMC) – has seen an average year-on-year reduction in price of 20.5 percent, from $1,160/kWh in 2010 to $176/kWh in 2018. While these numbers might look appealing, they don’t portray the full picture».
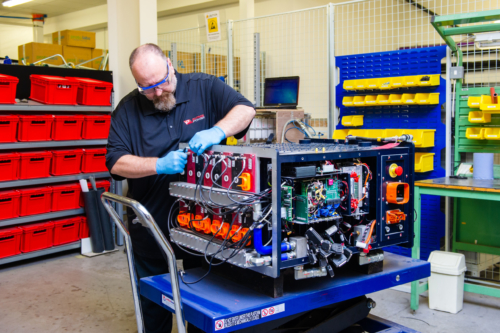
Little volume left available
«With consumer automotive companies – added Mr Schey – expecting to purchase the vast majority of foreseeable cell production in the coming years, there will be little volume left available for the smaller commercial vehicle market and getting hold of cells will become correspondingly more expensive. There are also legitimate concerns around the security of supply of cobalt – a critical element used in the production of lithium ion cells. So, while production volumes are increasing at impressive rates, and an army of engineers around the globe are working on reducing cell cobalt content, cost will continue to be a challenging factor for some years to come. Indeed, cells typically represent 50-75 percent of the cost of the total battery pack».